Zautomatyzowane planowanie i kontrola produkcji z MES

Systemy zarządzania produkcją (MES) pozwalają precyzyjnie zaplanować wszystkie procesy produkcyjne, monitorować je w czasie rzeczywistym i systematycznie optymalizować. Dlaczego są tak ważne? Ponieważ znane dotąd fabryki już dawno przestały istnieć i przekształciły się w zaawansowane technologicznie centra usługowe. Rozwój ten wymaga nowych koncepcji zarządzania produkcją, które pozwolą szybko i elastycznie reagować na zmiany w produkcji. Jak zatem działa system MES? Czy możliwa jest integracja MES z ERP?
Co to jest system MES?
MES to skrót od nazwy Manufacturing Execution System. Systemy MES są stosowane w obszarze operacyjnego zarządzania produkcją. Wspierają one w sposób kompleksowy zadania związane z planowaniem i sterowaniem procesami produkcyjnymi. Wiąże się to z importem wszystkich istotnych danych produkcyjnych w ramach następujących procesów:
- gromadzenia danych maszynowych - w celu automatycznego importu danych maszynowych,
- pozyskiwania danych osobowych - do kontrolowania planowania zasobów ludzkich,
- pozyskiwania danych jakościowych - dla zintegrowanego zarządzania jakością,
- gromadzenia danych procesowych - w celu monitorowania kluczowych parametrów procesu.
System MES wykorzystuje wszystkie agregowane informacje, aby przedstawić cyfrowy obraz aktualnego stanu produkcji. Zdarzenia produkcyjne stają się natychmiast widoczne - z ujawnionymi błędami planowania i możliwościami optymalizacji. Można więc powiedzieć, że system MES jest interfejsem pomiędzy dotychczasowym systemem ERP, a systemami automatyzacji procesów. Dzięki temu zapewnia on z jednej strony pozyskiwanie ogromnej ilości danych z procesów produkcyjnych, a z drugiej system MES kontroluje również realizację bieżącego planowania, uwzględniając informacje zwrotne otrzymywane z procesów produkcyjnych.
Wskaźnik do monitorowania produkcji
System MES konsoliduje dane dotyczące produkcji w postaci serii kluczowych wskaźników wydajności (KPI). Obejmują one zarówno wskaźniki związane ze stanowiskiem pracy i maszynami, jak i kompleksowe wskaźniki służące do oceny organizacji procesów produkcyjnych. KPI umożliwiają przejrzystą ocenę postępów i stopnia realizacji celów produkcyjnych, a także krytycznych czynników sukcesu. Wskaźniki te obejmują następujące elementy:
- czas realizacji,
- przestrzeganie terminów dostaw,
- wykorzystanie i wydajność maszyn, mające na celu ocenę wolnych mocy produkcyjnych,
- szacowanie odsetka odrzutów,
- określanie wydajności procesu (OEE - Overall Equipment Effectiveness).
W jaki sposób system MES współdziała z systemem ERP
W procesie przepływu pracy system ERP uruchamia się wcześniej niż system MES. Dzieje się tak, ponieważ system MES bazuje na informacjach pochodzących z systemu ERP. System ERP wykorzystuje agregowane informacje do sporządzenia przybliżonego planu. Oznacza to, że choć zamówienia są przypisane do zmian, to nie są przypisane do dokładnych czasów produkcji. Przydzielanie konkretnych zasobów odbywa się w drugim kroku - na etapie tzw. planowania szczegółowego.
Co istotne, niektóre systemy ERP są w stanie wspierać etap planowania szczegółowego. Mogą one przykładowo podzielić zamówienia na operacje, przypisać maszyny i personel oraz zaplanować je na dokładny czas w procesie produkcyjnym. Nie uwzględniają jednak zdarzeń produkcyjnych, które mogą wystąpić niespodziewanie, takich jak brak personelu, przestój maszyny lub uszkodzenie narzędzi. W tym właśnie miejscu rozwiązania MES mają wyraźną przewagę, ponieważ monitorują procesy produkcyjne w czasie rzeczywistym.
W przypadku systemów MES kolejność, w jakiej zamówienia są realizowane oraz konkretne procesy robocze są określane przez centrum kontroli. Wymagane zasoby, takie jak maszyny i odpowiednio wykwalifikowani pracownicy, są przypisywane do poszczególnych operacji, przy czym są one stale porównywane z rzeczywistą sytuacją produkcyjną. W ten sposób uzyskuje się szczegółowy plan rozmieszczenia wszystkich pracowników, maszyn, narzędzi i materiałów. Istotne dane pochodzące z systemu MES są z kolei przekazywane do systemu ERP. Dzięki temu powstaje system sterowania ze sprzężeniem zwrotnym, w którym dwa systemy gromadzenia informacji i optymalizacji procesów są ze sobą optymalnie zintegrowane.
Źródło: proALPHA Polska
Redaktor: MRR
- Roboty mobilne - przegląd rynku 2020
- Praktyczna wiedza od ekspertów Beckhoff
- Robotyzacja zakładów mięsnych: Moda czy innowacja?
- 212 mln zł na automatyzację i robotyzację dla MŚP
- Hybrydowe zgrzewanie punktowe materiałów MPMS/MPC
- P-Weld – Zrobotyzowane Rozwiązania w Spawaniu
- Ulga na robotyzację - do kiedy można skorzystać?
- Zrobotyzowany przegląd targów branżowych 2025
- Raport: Przegląd Rynku Robotów Współpracujących (Cobotów)
- Raport: Rynek robotów mobilnych AGV i AMR w 2025
- Jak wybrać system ERP idealny dla firmy produkcyjnej?
- EMO Hannover 2025 – odwiedź centrum innowacji przemysłowych
- Rynek robotów współpracujących — perspektywy na rok 2025
- Dyrektywa maszynowa: Co zmienia się od 2027 w robotyzacji?
- Rynek robotów przemysłowych: silne odbicie w 2025?
- Wsparcie procesu robotyzacji w Polsce. Rekomendacje PIE
- OEE i śledzenie przestojów
- TOOLEX i ExpoWELDING 2025. Katowice znów stolicą przemysłu
- Współpraca BMW i SEW-EURODRIVE
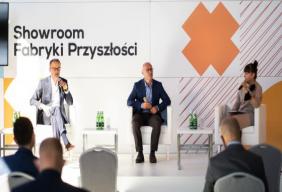
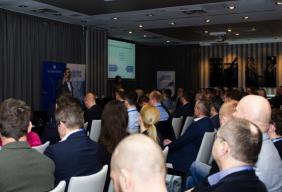
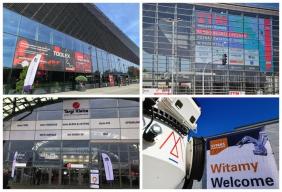

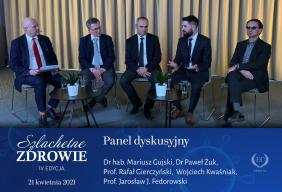
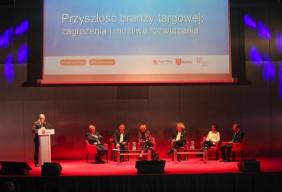