Sześć kroków do zbudowania cyfrowej fabryki
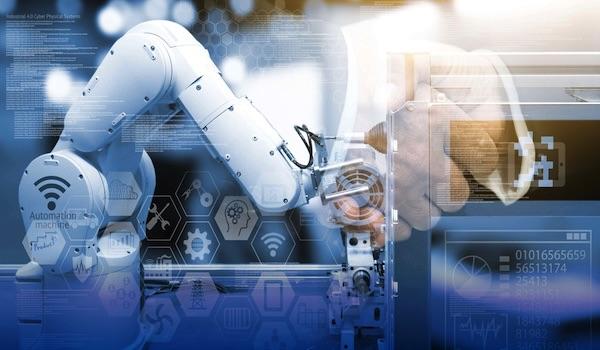
W tym przewodniku przedstawiono sześć podstawowych kroków do zbudowania cyfrowej fabryki, ilustrując, w jaki sposób producenci, konstruktorzy maszyn, integratorzy systemów i integratorzy systemów mogą współpracować, aby stworzyć bezproblemowe, przyszłościowe operacje.
Cyfrowa fabryka nie jest celem samym w sobie - jest narzędziem do osiągnięcia elastyczności, wydajności i innowacyjności w produkcji. Przedsiębiorstwa muszą dostosować się do zmieniających się rynków, trendów innowacyjnych i presji kosztowej. Cyfrowa fabryka stanowi podstawę tej zdolności adaptacyjnej, umożliwiając firmom z różnych branż - w tym żywności i napojów, farmaceutyków, higieny osobistej i motoryzacji - rozwój w konkurencyjnym środowisku.
1. Generowanie pomysłów i projektowanie
Każda cyfrowa fabryka zaczyna się od koncepcji — niezależnie od tego, czy jest to nowy produkt, czy zoptymalizowany proces produkcyjny. Na tym etapie nacisk kładziony jest na dostosowanie wymagań dotyczących produktów do możliwości produkcyjnych, zapewnienie wydajności, zgodności i zdolności adaptacyjnych. Współpraca z doświadczonymi partnerami jest niezbędna, aby wypełnić lukę między projektowaniem produktu a realiami produkcyjnymi, umożliwiając firmom tworzenie systemów, które spełniają potrzeby rynku, jednocześnie budując elastyczność na przyszłość.
Kluczowe obszary koncentracji:
- Zdefiniuj wymagania dotyczące produktów i procesów zgodnie z trendami rynkowymi i przepisami.
- Określ elastyczny sprzęt, który może dostosować się do zmian produktu i szybkich zmian.
- Zapewnij zgodność z globalnymi i regionalnymi standardami.
- Współpracuj z zaufanymi dostawcami, którzy wnoszą specjalistyczną wiedzę branżową.
Jeśli weźmiemy za przykład produkcję samochodów, firmy muszą wziąć pod uwagę wymagania dotyczące komponentów ogniw paliwowych i konstrukcji akumulatorów, aby spełnić różne normy dotyczące recyklingu, bezpieczeństwa i emisji CO2, w zależności od rynku.
Z drugiej strony, producenci napojów również stoją przed wyjątkowymi wyzwaniami. Elastyczna linia produkcyjna może obsługiwać butelki w kształcie jabłek na sok w jednym regionie i standardowe opakowania kartonowe w innym. Faza projektowania ma kluczowe znaczenie dla zapewnienia zgodności z lokalnymi normami recyklingu.
2. Symulacja: od koncepcji do wirtualnego bliźniaka
Symulacja jest kamieniem węgielnym cyfrowej fabryki. Modelując procesy w środowisku wirtualnym, producenci mogą testować, walidować i optymalizować systemy produkcyjne przed fizycznym wdrożeniem. Takie podejście zmniejsza ryzyko i koszty, a także skraca czas wprowadzania produktów na rynek.
Korzyści z symulacji:
- Korzystaj z technik software-in-the-loop (SiL) i hardware-in-the-loop (HiL), aby weryfikować koncepcje.
- Twórz cyfrowe bliźniaki, aby naśladować rzeczywiste procesy i optymalizować scenariusze.
- Symuluj zaawansowane interakcje i zachowania.
- Skróć cykle planowania i projektowania nawet o 25%.
W branżach takich jak motoryzacja, w których cykle życia produktów się skracają, a cykle innowacji przyspieszają, symulacja zapewnia elastyczność niezbędną do utrzymania konkurencyjności. Wirtualny bliźniak linii produkcyjnej akumulatorów do pojazdów elektrycznych umożliwia producentom testowanie przepływów pracy, optymalizację obsługi materiałów i identyfikowanie potencjalnych wąskich gardeł przed zainwestowaniem w sprzęt. W branży kosmetycznej, na przykład przy projektowaniu nowej szminki można testować różne preparaty i konfiguracje produkcyjne przed próbami fizycznymi.
3. Wirtualne uruchomienie
Wirtualne uruchomienie opiera się na symulacji, umożliwiając testowanie całych systemów produkcyjnych w środowisku wirtualnym. Gwarantuje to, że potencjalne problemy zostaną zidentyfikowane i rozwiązane przed rozpoczęciem fizycznego uruchomienia.
Zastosowania wirtualnego uruchomienia:
- Weryfikuj koncepcje produkcyjne pod kątem elastyczności i skalowalności.
- Generuj precyzyjne specyfikacje dla integratorów systemów, aby zmniejszyć niejednoznaczność.
- Przeprowadzaj wirtualne testy, aby udoskonalić procesy i uniknąć kosztownych awarii maszyn.
Wykorzystując wirtualne uruchomienie, producenci mogą osiągnąć czas rozruchu krótszy nawet o 40% w porównaniu z tradycyjnymi podejściami, umożliwiając szybkie reagowanie na wymagania rynku.
Firma farmaceutyczna może wykorzystać wirtualne uruchomienie do udoskonalenia produkcji spersonalizowanej linii medycznej, identyfikując potencjalne problemy z przepływem materiałów i czasem pracy maszyny bez przerywania bieżących operacji.
4. Inżynieria i automatyzacja
Inżynieria integruje zasady projektowania z technologiami automatyzacji w celu tworzenia połączonych i inteligentnych systemów. Powodzenie tego kroku zależy od połączenia historycznie odrębnych światów technologii operacyjnej (OT) i technologii informacyjnej (IT). Systemy cyberfizyczne, takie jak przemysłowe systemy sterowania i robotyki lub systemy wizyjne w połączeniu z algorytmami, odgrywają kluczową rolę w tej integracji. Umożliwienie bezproblemowej komunikacji między sprzętem, czujnikami i oprogramowaniem zapewnia, że wszystkie komponenty są ze sobą połączone i mogą efektywnie udostępniać dane. Na przykład czujniki wbudowane w maszyny generują dane, które muszą być interpretowane i wykorzystywane w znaczący sposób, umożliwiając systemom "komunikowanie się ze sobą" i spójną pracę w celu wspierania ogólnego działania cyfrowej fabryki.
Kluczowe cele inżynieryjne:
- Zautomatyzuj do 80% programowania maszyn dzięki zintegrowanym narzędziom inżynierskim.
- Osiągnij wymianę danych w czasie rzeczywistym między czujnikami a systemami korporacyjnymi.
- Optymalizuj procesy dzięki adaptacyjnym, samouczącym się systemom, które reagują na zmieniające się warunki.
- Zapewnij łączność z szeroką gamą urządzeń i protokołów.
Włączenie IT do automatyzacji umożliwia producentom osiągnięcie nowego poziomu przejrzystości operacyjnej i kontroli.
Weźmy pod uwagę przypadek producentów opakowań, którzy stoją przed wyzwaniami związanymi z możliwością dostosowania maszyn podczas przełączania między różnymi materiałami. Integrując komponenty automatyki i sterowniki PLC firmy OMRON z narzędziami inżynieryjnymi firmy Dassault Systèmes, można osiągnąć bezproblemową komunikację między czujnikami a oprogramowaniem. Umożliwia to automatyczne dostosowanie ustawień maszyny w oparciu o zmiany materiału, co prowadzi do zmniejszenia ilości odpadów i poprawy wydajności produkcji.
5. Fizyczne uruchomienie i rozruch
Przejście z systemów wirtualnych na fizyczne wymaga starannej koordynacji, aby zapewnić bezproblemową konfigurację i szybki czas uruchomienia. Ten krok skupia się na montażu, testowaniu i uruchamianiu linii produkcyjnych w jak najkrótszym czasie.
Priorytety w zakresie fizycznego uruchomienia:
- Zintegruj wstępnie zweryfikowane systemy, aby zminimalizować korekty metodą prób i błędów.
- Wdrażaj modułowy sprzęt, aby ułatwić skalowalność i rekonfigurację.
- Korzystaj z danych konserwacji predykcyjnej, aby zapobiegać przestojom podczas rozruchu.
Branże takie jak motoryzacja i dobra konsumpcyjne, w których często dochodzi do zmian sezonowych i dostosowywania, korzystają z elastycznych systemów, które umożliwiają szybkie przezbrajanie i wdrażanie.
Jednym z typów firm, który ilustruje ten problem, jest producent elektroniki, który może zwiększyć produkcję nowej linii montażowej PCB w ciągu kilku tygodni, a nie miesięcy, ponieważ wszystkie konfiguracje i testy są wykonywane wirtualnie.
6. Obsługa, konserwacja i ciągła optymalizacja
Cyfrowa fabryka rozwija się dzięki ciągłemu doskonaleniu. Gromadzenie, monitorowanie i analiza danych w czasie rzeczywistym pozwalają producentom optymalizować swoje systemy, przewidywać potencjalne awarie i dostosowywać się do przyszłych wymagań.
Strategie ciągłego doskonalenia:
- Monitoruj wydajność sprzętu za pomocą narzędzi do konserwacji predykcyjnej i monitorowania stanu.
- Symuluj nowe materiały lub procesy w środowisku wirtualnym przed wdrożeniem.
- Wykorzystaj szczegółowe informacje z cyfrowych bliźniaków, aby zwiększyć ogólną efektywność sprzętu (OEE).
Weźmy na przykład przemysł farmaceutyczny, w którym możliwość symulowania i wytwarzania niestandardowych preparatów w optymalnej dawce dla każdego pacjenta stanowi duży przełom w wydajności i personalizacji.
Z drugiej strony, w produkcji żywności, fabryka produkująca tabliczki czekolady może zoptymalizować zużycie energii i zmniejszyć ilość odpadów, wykorzystując dane w czasie rzeczywistym dotyczące temperatury i wilgotności maszyny.
Wprowadzenie
Budowa cyfrowej fabryki wymaga czegoś więcej niż tylko technologii. Wzywa do strategicznej współpracy, zaufania i otwartości między wszystkimi zainteresowanymi stronami. Fundamentem tej podróży jest połączenie IT i OT – dwóch światów, które historycznie działały w silosach.
Łączenie IT i OT:
- Stwórz solidne systemy cyberfizyczne, aby połączyć czujniki, maszyny i oprogramowanie dla przedsiębiorstw.
- Upewnij się, że wszystkie komponenty generują użyteczne dane i bezproblemowo się komunikują.
- Zintegruj systemy samouczące się, aby zoptymalizować kontrolę jakości, konserwację sprzętu i projektowanie produktów.
Udana cyfryzacja zależy również od stworzenia ekosystemów współpracy. Konstruktorzy maszyn, integratorzy systemów i użytkownicy końcowi muszą dostosować swoje cele i dzielić się wiedzą. Może to obejmować partnerstwo z instytucjami akademickimi, start-upami, a nawet konkurencją.
Rola zaufania:
- Otwarte systemy umożliwiają innowacje, ale wymagają wzajemnego zaufania.
- Partnerzy muszą być chętni do dzielenia się spostrzeżeniami i wiedzą bez obawy o utratę przewagi konkurencyjnej.
Firmy OMRON i Dassault Systèmes ściśle ze sobą współpracują, aby połączyć swoją wiedzę z zakresu OT i IT, tworząc bezproblemowe rozwiązanie dla cyfrowej fabryki zgodne z ramami ISA-95.
Przyszłość cyfrowych fabryk
Cyfrowe fabryki to szansa na transformację dla producentów. Dzięki symulacji, wirtualnemu uruchamianiu i połączonej automatyzacji firmy mogą zmniejszyć ryzyko swoich projektów, przyspieszyć innowacje i osiągnąć nowy poziom elastyczności. Jednak prawdziwy potencjał cyfrowej fabryki tkwi w jej zdolności do tworzenia ciągłego cyklu doskonalenia. Droga do cyfryzacji jest złożona i wymaga od producentów nawigacji w zakresie integracji zaawansowanych technologii i procesów. Sukces zależy od wyboru doświadczonych partnerów, którzy wnoszą sprawdzoną wiedzę w swoich dziedzinach. Dzięki ścisłej współpracy między interesariuszami technologii operacyjnej (OT) i technologii informacyjnej (IT) producenci mogą budować odporne i zrównoważone systemy. Systemy te są praktyczne i zaprojektowane tak, aby dostosować się do wymagań rynku i wymogów regulacyjnych.
#MakeitExcellent https://industrial.omron.eu/make-it-excellent
Źródło: Omron
Zdjęcie: Omron
- Roboty mobilne - przegląd rynku 2020
- Praktyczna wiedza od ekspertów Beckhoff
- Robotyzacja zakładów mięsnych: Moda czy innowacja?
- 212 mln zł na automatyzację i robotyzację dla MŚP
- Hybrydowe zgrzewanie punktowe materiałów MPMS/MPC
- P-Weld – Zrobotyzowane Rozwiązania w Spawaniu
- Ulga na robotyzację - do kiedy można skorzystać?
- Zrobotyzowany przegląd targów branżowych 2025
- Raport: Przegląd Rynku Robotów Współpracujących (Cobotów)
- Raport: Rynek robotów mobilnych AGV i AMR w 2025
- Moduły liniowe Bosch Rexroth przyspieszają automatyzację
- Jak wybrać system ERP idealny dla firmy produkcyjnej?
- EMO Hannover 2025 – odwiedź centrum innowacji przemysłowych
- Rynek robotów współpracujących — perspektywy na rok 2025
- Dyrektywa maszynowa: Co zmienia się od 2027 w robotyzacji?
- Rynek robotów przemysłowych: silne odbicie w 2025?
- Wsparcie procesu robotyzacji w Polsce. Rekomendacje PIE
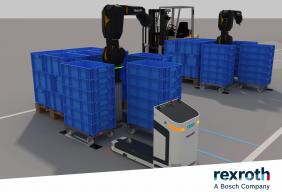

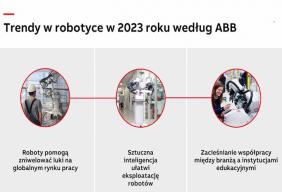
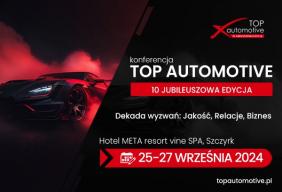
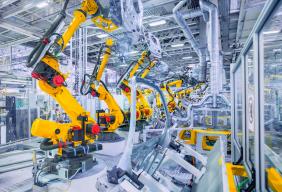
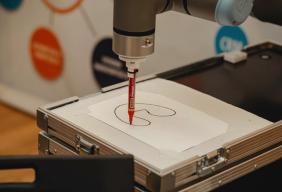