Jak maksymalizować wydajność produkcji?
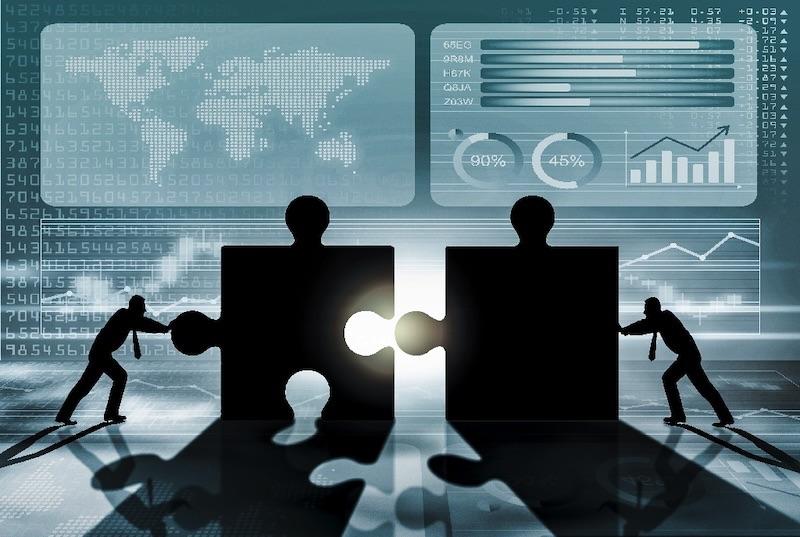
Jeśli chcesz dowiedzieć się jak maksymalizować wydajność i minimalizować przestoje na produkcji, koniecznie musisz zapoznać się z dalszą częścią artykułu.
W dzisiejszym dynamicznym środowisku biznesowym, skuteczne planowanie produkcji stanowi kluczowy element sukcesu przedsiębiorstwa. Procesy produkcyjne są nieustannie narażone na różnorodne wyzwania, takie jak zmienne zapotrzebowanie rynkowe, fluktuacje cen surowców czy nieprzewidywalne zakłócenia w łańcuchu dostaw. W tym kontekście, umiejętne zarządzanie planowaniem produkcji staje się nie tylko niezbędne, lecz wręcz nabiera wymiaru o charakterze strategicznym.
Planowanie produkcji - na czym polega?
Planowanie produkcji to kompleksowy proces, który stanowi niezwykle istotny element skutecznego zarządzania przedsiębiorstwem produkcyjnym. Polega on na strategicznym ustalaniu, kiedy, jakie i w jakich ilościach produkty powinny być wytwarzane, aby spełnić wymagania rynku. W skrócie, to próba optymalnego dostosowania zdolności produkcyjnych do zmieniającego się zapotrzebowania.
Planowanie produkcji uwzględnia różnorodne czynniki, takie jak prognozowanie popytu, efektywność procesów, dostępność surowców oraz harmonogramowanie działań, mając na celu minimalizację kosztów i maksymalizację efektywności. Właściwe planowanie produkcji to klucz do utrzymania konkurencyjności na rynku i skutecznego reagowania na dynamiczne zmiany w otoczeniu biznesowym.
Jakie czynniki wpływają na procesy prosukcyjne?
Procesy produkcyjne są podatne na wpływ różnorodnych czynników, które mogą istotnie kształtować ich efektywność i skuteczność. Ich przykładami są:
Zapotrzebowanie rynkowe
Fluktuacje w zapotrzebowaniu rynkowym mogą znacząco wpływać na planowanie produkcji. Ma to szczególne znaczenie w sektorach cechujących się sezonowością. Z tego względu właściwe dostosowywanie produkcji do zmieniających się potrzeb klientów jest kluczowe dla uniknięcia gromadzenia nadmiernej ilości zapasów lub doprowadzenia do sytuacji, gdy popyt przewyższy podaż.
Dostępność surowców
Braki surowców lub nagła zmiana ich dostępności może prowadzić do przestojów produkcyjnych. Stabilność w łańcuchu dostaw jest zatem kluczowym czynnikiem wpływającym na procesy produkcyjne.
Użycie odpowiednich technologii
Wykorzystanie nowoczesnych technologii, takich jak automatyzacja, robotyzacja czy sztuczna inteligencja, ma istotny wpływ na efektywność procesów produkcyjnych. Odpowiednio zastosowane i wdrożone innowacje technologiczne mogą bowiem zwiększyć wydajność i jakość produkcji. W kontekście tym warto także podkreślić rolę zintegrowanych systemów ERP do zarządzania produkcją, które znacząco ułatwiają planowanie prac oraz ich optymalizację.
Kadra pracownicza
Umiejętności, motywacja i zaangażowanie pracowników mają również bardzo ważne znaczenie dla efektywności procesów produkcyjnych. Odpowiednie szkolenia, system motywacyjny i zarządzanie personelem mogą znacząco poprawić wydajność.
Warunki środowiskowe
Wśród czynników wpływających na procesy produkcyjne nie można pominąć także warunków środowiskowych, takich jak temperatura, wilgotność czy czystość. Mogą one mieć wpływ na procesy produkcji, zwłaszcza w przypadku produkcji precyzyjnej czy związanej z elektroniką.
Zarządzanie łańcuchem dostaw
Efektywne zarządzanie dostawami surowców i komponentów również wpływa na płynność i wydajność produkcji. Opóźnienia czy braki w dostawach mogą prowadzić do przestoju linii produkcyjnych.
Polityka regulacyjna
Zmiany w przepisach regulacyjnych mogą wpływać na procesy produkcyjne, zwłaszcza jeśli wymagają dostosowania do nowych norm bezpieczeństwa czy standardów jakości.
Bez wątpienia zrozumienie istoty i ważności tych czynników oraz uwzględnianie ich rangi w procesie produkcji jest kluczowe dla utrzymania płynności procesów i osiągnięcia sukcesu w dynamicznym środowisku biznesowym.
Jak maksymalizować wydajność i minimalizować przestoje w przedsiębiorstwach produkcyjnych?
Maksymalizacja wydajności i minimalizacja przestojów w przedsiębiorstwach produkcyjnych wymaga zastosowania strategicznych podejść i skoncentrowania się na kilku ważnych obszarach.
1. Optymalizacja procesów produkcyjnych
Optymalizacja procesów produkcyjnych jest fundamentalnym krokiem w zapewnieniu efektywności działania przedsiębiorstwa. Skrupulatne badanie poszczególnych etapów produkcji pozwala na zidentyfikowanie potencjalnych obszarów problemowych, zwanych wąskimi gardłami. Wąskie gardła to miejsca, w których przepustowość procesu jest ograniczona, co wpływa na ogólną wydajność. Istotne jest, aby skupić się na kilku kluczowych aspektach:
Analiza etapów produkcyjnych
Szczegółowa analiza każdego etapu produkcji pozwala na zidentyfikowanie tych, w których proces może ulec opóźnieniom lub zakłóceniom. To podejście umożliwia lepsze zrozumienie całego przepływu pracy i pozwala na dokładne określenie, gdzie mogą wystąpić problemy.
Identyfikacja wąskich gardeł
Wyszukanie i zdefiniowanie wąskich gardeł jest kluczowe dla skutecznej optymalizacji procesów produkcyjnych. Mogą to być miejsca, gdzie konkretne maszyny, pracownicy lub surowce ograniczają ogólną przepustowość. Przykładowo, wykazanie, że określona maszyna jest częstym źródłem przestojów, umożliwia podjęcie działań naprawczych.
Wprowadzanie ulepszeń
Po zidentyfikowaniu wąskich gardeł konieczne jest wdrożenie planu naprawczego. Etap ten może obejmować modernizację sprzętu, zwiększenie liczby pracowników w kluczowych obszarach, czy też bardziej efektywne zarządzanie zapasami surowców. Ważne jest, aby rozwiązania były dostosowane do konkretnych potrzeb i problemów wykrytych podczas analizy.
Właściwa alokacja zasobów
Optymalizacja procesów produkcyjnych pozwala na lepsze wykorzystanie dostępnych zasobów, zarówno ludzkich, jak i technologicznych. Skrócenie czasu przestoju oraz eliminacja wąskich gardeł przekłada się bowiem bezpośrednio na zwiększenie efektywności i wydajności całego przedsiębiorstwa.
2. Wdrożenie systemu ERP
Wdrożenie systemu ERP (Enterprise Resource Planning) jest kolejnym kluczowym krokiem w dążeniu do maksymalizacji wydajności i minimalizacji przestojów w przedsiębiorstwach produkcyjnych. Systemy ERP integrują różne działy firmy, umożliwiając lepszą kontrolę nad procesami oraz zapewniając kompleksowe zarządzanie zasobami.
Warto pamiętać, że przed wdrożeniem systemu ERP konieczna jest szczegółowa analiza wszystkich procesów biznesowych. Pozwala to na zidentyfikowanie obszarów, w których system ERP może przynieść najwięcej korzyści. Warto również uwzględnić specyficzne potrzeby branżowe, produkcyjne oraz indywidualne potrzeby danego przedsiębiorstwa. Oprogramowanie powinno być skonfigurowane tak, aby idealnie współgrało z istniejącymi procesami produkcyjnymi, a także umożliwiało łatwe skalowanie w miarę rozwoju firmy.
Nie zapominajmy przy tym, że efektywne wykorzystanie oprogramowania ERP wymaga odpowiedniego przeszkolenia pracowników. Zorganizowanie szkoleń związanych z obsługą systemu jest więc niezwykle istotne dla podniesienia świadomości personelu w zakresie funkcjonalności oraz umiejętności korzystania z nowych narzędzi.
Bez wątpienia wdrożenie systemu ERP w przedsiębiorstwie produkcyjnym jest inwestycją w efektywność i konkurencyjność. Poprzez staranne dostosowanie, integrację i monitorowanie, firma może maksymalizować korzyści z tego zaawansowanego narzędzia zarządzania zasobami, przyczyniając się do redukcji przestojów i zwiększenia ogólnej wydajności procesów produkcyjnych.
3. Dokładne planowanie i prognozowanie produkcji
Precyzyjne planowanie produkcji, oparte na rzetelnych prognozach popytu, pozwala unikać nadmiernego zatowarowania lub niedoborów w magazynie. To kluczowe dla zminimalizowania przestojów i utrzymania płynności produkcji.
Skuteczne planowanie zaczyna się od gruntownej analizy rynku i trendów. Monitorowanie zmian w zachowaniach konsumentów, technologii i konkurencji pozwala na stworzenie precyzyjnych prognoz popytu, co jest niezbędne do odpowiedniego dostosowywania produkcji.
W procesie tym istotne jest wykorzystanie zaawansowanych narzędzi do prognozowania, takich jak modele statystyczne czy sztuczna inteligencja. Narzędzia te są w stanie uwzględnić szereg czynników, co czyni prognozy bardziej wiarygodnymi.
Poza tym warto pamiętać, że plany produkcji wymagają ciągłej optymalizacji – powinny być elastyczne, umożliwiając szybką adaptację do zmieniających się warunków rynkowych. Elastyczność pozwala unikać nadmiarów poprzez dostosowywanie produkcji do rzeczywistego zapotrzebowania, co ma bezpośrednie przełożenie na minimalizację przestojów oraz redukcję zapasów.
Skuteczne planowanie produkcji wymaga również współpracy z dostawcami i partnerami biznesowymi. Informowanie pozyskane od nich pozwalają na lepsze dostosowywanie łańcucha dostaw do aktualnych potrzeb, co w konsekwencji wpływa na płynność całego procesu.
4. Dokładne monitorowanie i właściwe utrzymanie sprzętu produkcyjnego
Maksymalizowanie wydajności w przedsiębiorstwach produkcyjnych wymaga nie tylko optymalizacji procesów, ale także dbałości o stan techniczny używanych maszyn i urządzeń. Regularne monitorowanie i konserwacja sprzętu są kluczowe dla minimalizacji awarii oraz utrzymania płynności produkcji.
Zaplanowane i regularne przeglądy techniczne maszyn pozwalają na wykrywanie potencjalnych problemów przed ich eskalacją. Konserwacja, obejmująca zarówno czyszczenie, smarowanie, jak i wymianę zużytych części, może znacząco przedłużyć żywotność sprzętu. Skrupulatne prowadzenie historii konserwacji umożliwia również określenie optymalnych interwałów między przeglądami.
Na szczęście w obecnych czasach nie trzeba wszystkich tych zadań wykonywać ręcznie. Zastosowanie zaawansowanych systemów monitorowania parametrów pracy maszyn pozwala na bieżącą analizę ich efektywności. Monitoring takich wskaźników jak temperatura, ciśnienie czy zużycie energii umożliwia szybkie reagowanie na ewentualne odchylenia, co z kolei minimalizuje ryzyko nieplanowanych przestojów.
Warto także mieć świadomość, że dążąc do maksymalizowania wydajności i minimalizowania przestojów w przedsiębiorstwie produkcyjnym, konieczne jest stałe inwestowanie w posiadany park maszynowy. Może to przyczynić się do zwiększenia ogólnej efektywności produkcji. Co więcej, nowoczesne maszyny często charakteryzują się większą niezawodnością, szybszymi czasami cyklu oraz łatwiejszą integracją z systemami ERP.
Skuteczne planowanie produkcji to klucz do sukcesu przedsiębiorstwa produkcyjnego. Procesy te są narażone na liczne wyzwania, takie jak zmienne zapotrzebowanie rynkowe czy nieprzewidywalne zakłócenia w łańcuchu dostaw. Optymalizacja procesów, wdrożenie systemu ERP, precyzyjne planowanie i prognozowanie produkcji, a także monitorowanie oraz utrzymanie sprzętu są kluczowymi obszarami, na których przedsiębiorstwa powinny się skoncentrować. Te strategie pomagają minimalizować przestoje, zwiększać efektywność i dostosować się do dynamicznych warunków rynkowych.
Źródło: proALPHA Polska
Zdjęcie: proALPHA Polska
- Roboty mobilne - przegląd rynku 2020
- Praktyczna wiedza od ekspertów Beckhoff
- Robotyzacja zakładów mięsnych: Moda czy innowacja?
- 212 mln zł na automatyzację i robotyzację dla MŚP
- Hybrydowe zgrzewanie punktowe materiałów MPMS/MPC
- P-Weld – Zrobotyzowane Rozwiązania w Spawaniu
- Ulga na robotyzację - do kiedy można skorzystać?
- Zrobotyzowany przegląd targów branżowych 2025
- Webinary Beckhoff – dostępne online
- Estun inwestuje w Polsce
- Raport: Przegląd Rynku Robotów Współpracujących (Cobotów)
- Jak zwiększyć efektywność AGV? Radarowe czujniki w akcji
- Raport: Rynek robotów mobilnych AGV i AMR w 2025
- Nowe funkcje usprawniają pracę inżynierów i programistów
- Monitorowanie i optymalizacja flot robotów
- Konkretnie o Automatyzacji – praktyczne spotkania dla przemysłu
- Moduły liniowe Bosch Rexroth przyspieszają automatyzację
- Jak wybrać system ERP idealny dla firmy produkcyjnej?
- EMO Hannover 2025 – odwiedź centrum innowacji przemysłowych
- Automatyzacja sprzątania z KIRA CV
- Rekordowe targi robotyki i automatyzacji automatica 2025
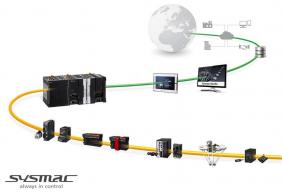
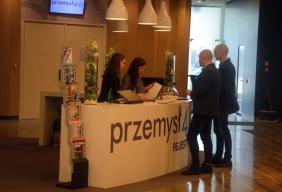
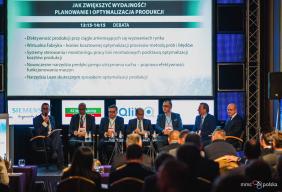

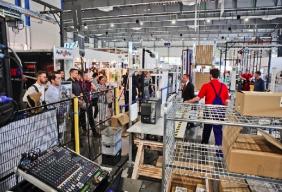
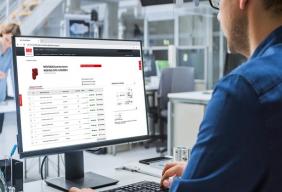