Automatyzacja obróbki ręcznej przy pomocy gniazda obróbczego
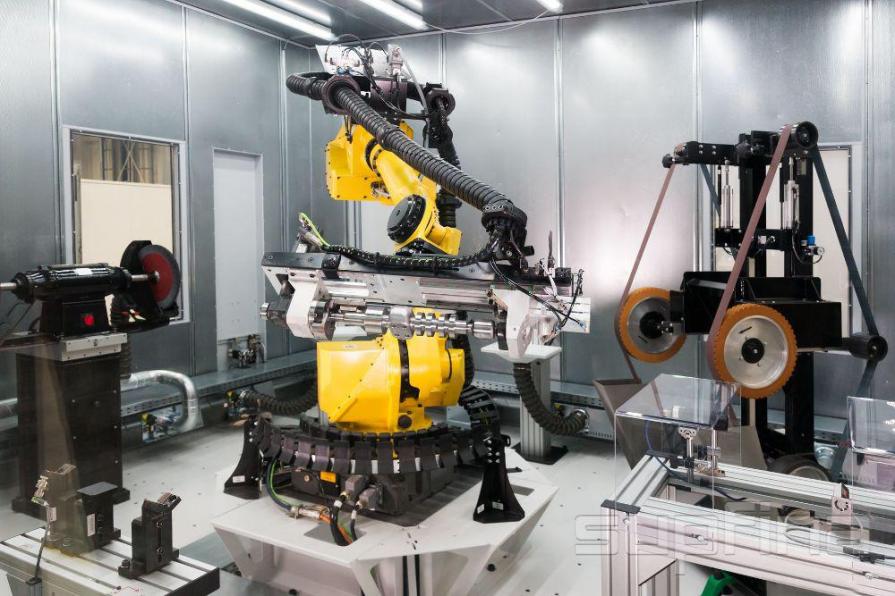
Proces gratowania i wykańczania powierzchni różnych części – automatyzacja obróbki ręcznej za pomocą zrobotyzowanego i uniwersalnego gniazda obróbczego.
Co to jest gratowanie i jakie przynosi efekty
Gratowanie to usuwania ostrych krawędzi i zadziorów w celu uzyskania powierzchni o poprawionych parametrach takich jak chropowatość i gładkość powierzchni, usuwanie nierówności, itd. Gratowanie umożliwia uzyskanie powierzchni odpowiedniej jakości. Znane są różne sposoby poprawy jakości powierzchni jak np. obróbka ręczna, proces ręczno-maszynowy, metoda wibrościerna, wykorzystanie past ściernych, proces magneto-ścierny, obróbka elektro-chemiczna czy proces termiczny.
Ręczny proces gratowania jest bardzo żmudny, wymaga dużo czasu i jest niedoskonały, ponieważ umiejętności operatora wpływają znacząco na jego wynik. Obróbka ręczna jest nadal często stosowana i wynosi ok. 20% produkcji seryjnej, a przy produkcji jednostkowej wartość ta jest znacznie większa. Proces ręcznego gratowania często występuje w przemyśle samochodowym, lotniczym, medycznym, meblarskim, maszynowym, jubilerskim, przy produkcji narzędzi precyzyjnych, przy produkcji okularów.
Gratowanie i wykańczania powierzchni to m.in.: zatępianie krawędzi, czyszczenie i szczotkowanie, frezowanie, szlifowanie, polerowanie, dogładzanie (superfinish).
Obróbka wykańczająca powierzchni i proces dogładzania (SUPERFINISH)
Po procesie gratowania często stosuje się obróbką wykańczającą. Obróbka wykańczająca jest ostateczną fazą procesu obróbki i stosuje się ją, aby uzyskać wysoką jakość obrabianej części zgodną z wymaganiami dotyczącymi dokładności wymiarowej, błędów kształtu i chropowatości powierzchni.
Mamy 3 podstawowe typy obróbki wykańczającej:
- Bardzo dokładna obróbka
- Obróbka ostateczna
- Obróbka by uzyskać wysoką jakość powierzchni np. polerowane , dogładzanie, dokładne szlifowanie, itp.
Sposoby wykańczania powierzchni są dokładnie opisane w literaturze, dlatego warto skupić się na procesie dogładzania powierzchni, czyli na obróbce superfinish. Proces superfinish to proces dogładzania oscylacyjnego (dogładzanie krótko skokowe) – obróbka wygładzania powierzchni, dzięki której uzyskuje się chropowatości Rz 0,4 ÷ 0,01 (klasa gładkości 11 ÷ 14).
Dogładzanie powierzchni realizowane jest z wykorzystaniem narzędzi ściernych takich jak węglik krzemu (SiC) przy obróbce aluminium i żeliwa, a do obróbki stali stopów miedzi i obróbki zgrubnej stosuje się stopy aluminium. Proces dogładzania obejmuje powierzchnie pozostawione po poprzedniej obróbce.
Dogładzanie obejmuje przynajmniej trzy ruchy, w tym co najmniej jeden oscylacyjny. Dogładzanie polega na usunięciu pików chropowatości i można tym sposobem uzyskać Ra 0,01μm.
Poniżej przedstawiony został schemat obróbki oscylacyjnej.
![]() |
Zrobotyzowane gniazdo obróbcze
Firma SUPFINA oferuje uniwersalne i elastyczne gniazdo obróbcze, które może zastąpić obróbkę ręczną i tym samym pomóc zautomatyzować proces obróbki.
Zrobotyzowane gniazdo obróbcze oferuje różne operacje obróbcze jak m.in.: oczyszczenie powierzchni, zatępianie krawędzi, dogładzanie oscylacyjne (superfinish), gratowanie, szlifowanie, polerowanie, frezowanie, znakowanie, pomiar optyczny , kontrola wizualna itp.
Przykładowe konfiguracje mocowania i obróbki części:
- część obrabiana w uchwycie robota i podawana jest na poszczególne stacje obróbkowe
- część obrabiana na stole, narzędzia pobierane przez robota ze stacji obróbkowych i wykorzystywane do obróbki części
Przykłady konfiguracji zrobotyzowanego gniazda obróbczego: ładowanie / rozładowanie z wykorzystaniem przenośnika taśmowego, ręczny załadunek części i ręczna wymiana narzędzi, załadunek/wyładunek palet i obróbka rotacyjna części.
Zrobotyzowane gniazdo obróbcze umożliwia m.in.: automatyzację ręcznych procesów produkcyjnych, zastosowanie różnych procesów produkcyjnych w 1-nym gnieździe obróbczym, wykańczanie powierzchni po produkcji metodami przyrostowymi.
Zrobotyzowane gniazdo obróbcze jest uniwersalnym rozwiązaniem dzięki różnym możliwym procesom obróbczym, dowolnej konfiguracji gniazda, doborowi różnych narzędzi i ich wymienności, zarządzaniu produkcji z wykorzystaniem HMI.
Modułowa budowa może zostać wykorzystana do dowolnej konfiguracji zrobotyzowanego gniazda obróbczego w zależności od wymagań klientów.
W celu realizacji wymagań można zastosować roboty różnych producentów np. Fanuc (w standardzie), Kuka, ABB, Stäubli czy inne wg życzeń klienta.
Firma Isotek oferuje również (z wykorzystaniem CAD/CAM):
- program i rodzaj obróbki
- różne roboty w zależności od potrzeb
- różne czasy cykli
- rozwiązania wirtualne
Zrobotyzowane gniazdo obróbcze korzysta ze wsparcia firmy Supfina jak poniżej:
- inteligentny monitoring parametrów w czasie rzeczywistym - monitorowanie ich statusu
- dane archiwalne
- redukcję przestojów
- zwiększenie efektywności w produkcji
- zwiększenie opłacalności w produkcji
Proces obróbki może być następujący (przykłady):
- Pomiar części przed procesem obróbki
- Określenie wartości korekcyjnych (offsets)
- Wprowadzenie wartości korekcyjnych (offsets)
- Wybrany proces obróbki
Źródło: ISOTEK
Redaktor: EG
- Roboty mobilne - przegląd rynku 2020
- Praktyczna wiedza od ekspertów Beckhoff
- Robotyzacja zakładów mięsnych: Moda czy innowacja?
- 212 mln zł na automatyzację i robotyzację dla MŚP
- Hybrydowe zgrzewanie punktowe materiałów MPMS/MPC
- P-Weld – Zrobotyzowane Rozwiązania w Spawaniu
- Ulga na robotyzację - do kiedy można skorzystać?
- Zrobotyzowany przegląd targów branżowych 2025
- Webinary Beckhoff – dostępne online
- Estun inwestuje w Polsce
- Raport: Przegląd Rynku Robotów Współpracujących (Cobotów)
- Jak zwiększyć efektywność AGV? Radarowe czujniki w akcji
- Raport: Rynek robotów mobilnych AGV i AMR w 2025
- Nowe funkcje usprawniają pracę inżynierów i programistów
- Monitorowanie i optymalizacja flot robotów
- Konkretnie o Automatyzacji – praktyczne spotkania dla przemysłu
- Moduły liniowe Bosch Rexroth przyspieszają automatyzację
- Jak wybrać system ERP idealny dla firmy produkcyjnej?
- EMO Hannover 2025 – odwiedź centrum innowacji przemysłowych
- Automatyzacja sprzątania z KIRA CV
- Rekordowe targi robotyki i automatyzacji automatica 2025
- Rynek robotów współpracujących — perspektywy na rok 2025
- Dyrektywa maszynowa 2023/1230: Co zmienia się od 2027?
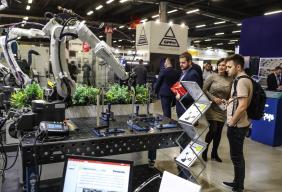

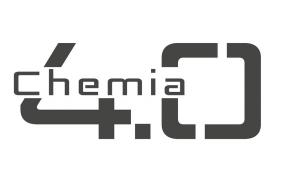
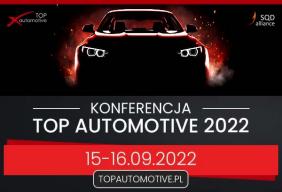
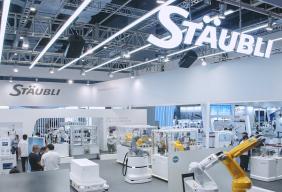
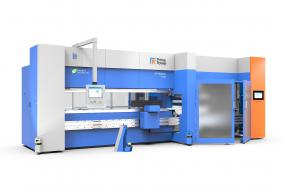