Zaawansowane systemy bezpieczeństwa dla robotów przemysłowych
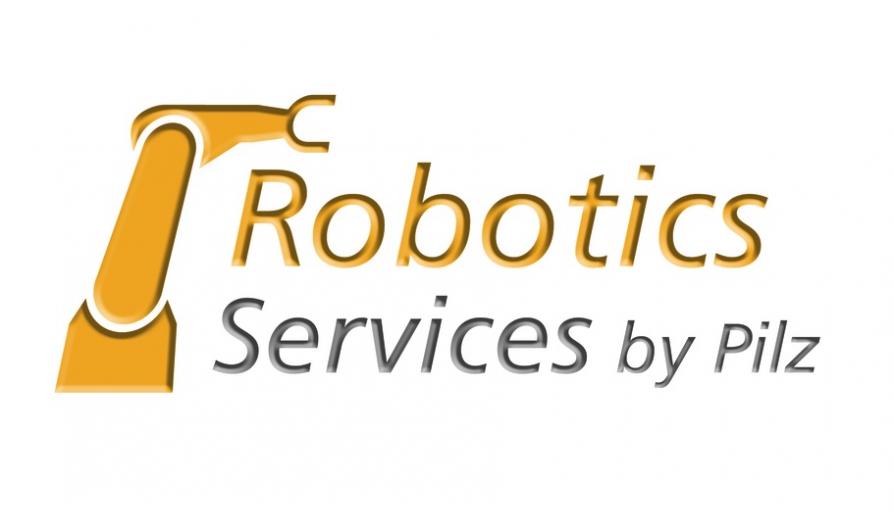
Zaawansowane systemy bezpieczeństwa dla robotów przemysłowych – nowe podejścia pracy z robotami w celu zwiększenia bezpieczeństwa oraz efektywności produkcji.
W obecnych czasach roboty przemysłowe wykorzystywane są w obszarach produkcyjnych, w których przedtem nigdy ich nie było. Klasyczne połączenie dużej zamkniętej przestrzeni poprzez wygrodzenie (klatkę) wraz z robotem w środku, nie jest już jedynym zastosowaniem robotów na liniach produkcyjnych. Coraz częściej ciężkie roboty przemysłowe spotykane są w obszarach, gdzie pracuje operator lub, gdzie operator ten musi mieć częsty dostęp. Coraz to bardziej zaawansowane systemy bezpieczeństwa tworzone przez producentów robotów ułatwiają integrację maszyn nie obniżając przy tym ich wydajności. W artykule tym przedstawione zostaną przykładowe zaawansowane funkcje bezpieczeństwa stosowane w dzisiejszych czasach przez całe środowisko przemysłowe.
Metody interakcji między człowiekiem a robotem
W celu łatwego zrozumienia zastosowania robotów warto pokrótce wspomnieć podstawowe funkcje bezpieczeństwa dla robotów przemysłowych. Głównym założeniem pracy na maszynach jest uniemożliwienie dostępu operatora do ruchów niebezpiecznych danej maszyny, lecz z uwzględnieniem współpracy pomiędzy operatorem oraz w tym przypadku robotem. Norma PN-EN ISO 10218-2 opisuje 4 metody współpracy pomiędzy operatorem a robotem:
- Monitorowanie zatrzymania: metoda polegająca na normalnej pracy robota bez człowieka, lecz gdy w strefie współpracy pojawi się operator robot zatrzymuje się w sposób bezpieczny np. poprzez funkcję STO (Safe Torque Off) lub SS1 (Safe Stop 1). Metoda ta jest klasycznym przykładem funkcji zatrzymania awaryjnego robota lub zatrzymania robota poprzez otwarcie drzwi bezpieczeństwa (zadziałanie czujnika bezpieczeństwa).
- Prowadzenie ręką: druga metoda interakcji między człowiekiem, a robotem, szczególnie przydatna podczas nauki/programowania robotów. Polega na możliwości sterowania robotem ze zmniejszoną prędkością przy użyciu tzw. teach pendanta – z reguły urządzenie posiadające przycisk trójpozycyjny (szczegóły dotyczące bezpieczeństwa tego urządzenia opisane są w pierwszej części normy PN-EN ISO 10218). Funkcje bezpieczeństwa, które powinny zostać zastosowane w tej metodzie to SLS (Safety Limited Speed) czy jedna z funkcji opisanych w pierwszej metodzie, które muszą zostać wykonane po przekroczeniu pozycji bezpiecznych robota lub po zwolnieniu przycisku trójpozycyjnego z kontrolera robota.
- Monitorowanie prędkości i separacji: metoda umożliwiająca pracę operatora w sąsiedztwie robota bez użycia wygrodzeń. Założeniem jest kontrolowanie pozycji operatora względem robota i dostosowanie tym samym prędkości robota. Standardowym rozwiązaniem używanym w tej metodzie jest połączenie skanera bezpieczeństwa z robotem. Podczas gdy operatora zbliża się do robota, prędkość robota maleje, aż do momentu, gdy robot musi się zatrzymać podczas pojawienia się człowieka w strefie „niebezpiecznej” zdeterminowanej poprzez ocenę ryzyka stanowiska. Funkcje bezpieczeństwa użyte w tej metodzie to np. SLS czy STO.
- Ograniczenie mocy i siły: metoda, którą można zastosować jedynie w specyficznych robotach tzw. cobotach. We wstępie zaznaczone zostało, że kontakt pomiędzy człowiekiem, a robotem jest niedopuszczalny. W przypadku tej metody uderzenie operatora przez robota jest możliwe pod pewnymi warunkami. Cobot powinien posiadać czujniki kontrolujące jego siłę i/lub moment. Podczas gdy, dopuszczalne siły (opisane w specyfikacji technicznej ISO/TS 15066) zostaną przekroczone w momencie kontaktu z człowiekiem robot powinien zatrzymać się w sposób bezpieczny np. funkcją STO.
Powyższe metody interakcji pomiędzy człowiekiem a robotem mają ułatwić integratorom robotów budowanie aplikacji w sposób bezpieczny wraz z możliwością skrócenia czasów przestojów robotów podczas ingerencji człowieka w strefę niebezpieczną maszyny. Rozwój technologii oraz coraz większa potrzeba skracania cykli produkcji wyrobów spowodowały stworzenie jeszcze bardziej zaawansowanych systemów bezpieczeństwa dla robotów opisanych poniżej.
SafeMove 2 – ABB
SafeMove2 jest to “funkcja” bezpieczeństwa stworzona przez firmę ABB oraz wykorzystywana w robotach przemysłowych ABB. SafeMove2 dostarcza rozwiązania eliminujące konieczność stosowania barier bezpieczeństwa, takich jak klatki bezpieczeństwa czy kurtyny świetlne. Zastosowanie tej funkcji polega na dołączeniu do kontrolera robota karty wraz z dedykowanych softwarem, co umożliwia zastosowanie dodatkowych funkcji w robocie:
- Bezpieczne strefy: umożliwia podział celi zrobotyzowanej na różne strefy bezpieczeństwa w zależności od instalacji,
- Bezpieczne zakresy osi: pozwalają na możliwość wykluczenia mechanicznych krańcówek na osiach na software’owe ograniczniki, zwiększając tym samym sterowanie oraz elastyczność podczas programowania bądź konserwacji,
- Bezpieczna prędkość robota: nadzoruje prędkość na określonym poziomie, co pozwala na bliższą pracę operatora obok robota,
- Cykliczne sprawdzanie hamulców: nadzoruje sprawdzanie hamulców z daną częstotliwością,
- Bezpieczny postój: nadzoruje zatrzymanie osi robota, co pozwala operatorowi na pracę przy robocie bez konieczności wyłączania całego układu napędów robota,
- oraz inne.
Plusami zastosowania takich rozwiązań są m. in. oszczędność miejsca w zakładzie, ułatwienie pracy człowiek/robot czy możliwość stosowania robota do praktycznie każdej możliwej aplikacji. SafeMove2 zapewnia bezpieczeństwo na poziomie Performance Level (d) w Kategorii 3, co jest zgodne z obowiązującymi normami.
![]() |
Dual Check Safety (DCS) – Fanuc
Fanuc do swoich robotów proponuje rozwiązanie bezpieczeństwa DCS opierające się na dwóch mikroprocesorach (redundancja systemu), które kontrolują pracę serwonapędów – ich rzeczywista prędkość porównywana z analizowanymi danymi układu. DCS nie wymaga dodatkowej instalacji kart czy urządzeń – wszystko odbywa się z pozycji programowej. Możliwe funkcje bezpieczeństwa do zastosowania to:
- Kontrola pozycji: definiowana wirtualna strefa robota 3D – po przekroczeniu pozycji kontrolowanej przez sterownik robot zatrzymuje się w sposób bezpieczny,
- Kontrola prędkości: kontrolowanie prędkości robota poprzez nadzorowanie prędkości danych osi lub całego układu kartezjańskiego robota zapewnia bezpieczniejszą konfigurację i obsługę procesów takich jak spawanie, zgrzewanie czy transport poprzez spowolnienie robota, gdy operator wejdzie do strefy pracy,
- Kontrola bezpiecznych stref: spowalnia robota bądź zatrzymuje w bezpiecznej strefie – wyznaczanie stref, gdzie robot powinien poruszać się np. ze zmniejszoną prędkością poprzez pracę operatora w danej strefie,
- Nadzorowanie narzędzia robota: zdefiniowanie odpowiednich pozycji bezpiecznych TCP, gdzie robot po ich osiągnięciu zatrzymuje bądź włącza/wyłącza się – możliwe do zaprogramowania 32 strefy oraz 10 różnych modeli kształtów,
- oraz inne.
Rozwiązanie bezpieczeństwa DCS według producenta spełnia wymagania Performance Level (d) zgodnie z ISO 13849-1. Do głównych zalet systemu należą: minimalizacja kosztów zastosowanego sprzętu bezpieczeństwa, możliwość sterowania strefami bezpiecznymi z innych urządzeń peryferyjnych w postaci np. bezpiecznych sterowników PLC, efektywne wykorzystanie przestrzeni wokół robota.
Functional Safety Unit – Yaskawa
Także japoński producent robotów Yaskawa oferuje w swoim portfolio moduł bezpieczeństwa do stosowania w robotach Motoman – Functional Safety Unit. Ulepszona jednostka FSU zapewnia niezawodną kontrolę strefy i pozycji narzędzia, monitorowanie pozycji robota i ograniczenie prędkości. Może to obniżyć koszty zapewnienia bezpieczeństwa redukując użyty w aplikacji sprzęt, zapewniając jednocześnie nowe możliwości, takie jak zadania współpracy robota z człowiekiem. Głównymi funkcjami bezpieczeństwa są:
- Monitorowanie limitu osi oraz ograniczonej przestrzeni: FSU oblicza wektor prędkości każdej osi (do 9 osi / jednostkę) w celu wyłączenia napędów, jeśli robot przekroczy wartości graniczne. Obliczenia uwzględniają czas opóźnienia w ograniczonej przestrzeni,
- Monitorowanie prędkości danych osi: określa maksymalną dopuszczalną prędkość pojedynczej osi robota, osi podstawy oraz stacji. Funkcja ta połączona jest z funkcją kontroli zatrzymania robota, jeżeli zaprogramowane zostanie ustawienie 0°/s, jako maksymalne ograniczenie prędkości,
- Monitorowanie zmiany narzędzia: monitorowanie czy do każdej instrukcji ruchu w zadaniu robota używane jest właściwe narzędzie (możliwość zdefiniowania do 16 narzędzi). Tryb uczenia monitoruje także, czy wybrane narzędzie pasuje do aktualnie używanego,
- Monitorowanie kąta narzędzia: FSU monitoruje kąt narzędzia w przestrzeni i zapewnia, że orientacja narzędzia pozostaje w obrębie stożka określonego przez limit kąta,
- oraz inne.
Funkcje FSU mogą być programowane przez dedykowane dwukanałowe wejścia/wyjścia w kontrolerze robota. Kontroler po zaprogramowaniu tworzy sumę kontrolną dla wszystkich danych oraz funkcji bezpieczeństwa. Moduł bezpieczeństwa FSU spełnia wymagania (co najmniej) Performance Level (d) zgodnie z ISO 13849-1 (dla funkcji e-stop/safety gate spełnia wymagania PL (e)). Zaletami systemu FSU są przed wszystkim eliminacja potrzeby stosowania mechanicznych blokad, które są podatne na zużycie i awarie oraz elastyczność systemu dla stosowania w różnego rodzaju aplikacjach.
Podsumowanie
Różnorodność przedstawionych powyżej tylko niektórych funkcji bezpieczeństwa dla robotów przemysłowych sprawia, że stosowanie klasycznego robota w klatce wraz z przyciskiem zatrzymania awaryjnego, jako główna funkcja bezpieczeństwa odeszło już dawno w niepamięć. Funkcje kontroli stref, osi, narzędzi czy prędkości robota stosowane są już powszechnie przez prawie wszystkich integratorów robotów przemysłowych. Nowoczesne zakłady produkcyjne oraz te, które chcą zwiększać swoją produktywność coraz częściej stosują aplikacje z robotami, gdzie wymagana jest szybkość robota w parze z szybkim przezbrojeniem czy serwisem. Nowoczesne funkcje bezpieczeństwa pozwalają na wdrażanie takich procedur przy zachowaniu bezpiecznej pracy dla operatorów/serwisantów. Trzeba pamiętać jednak, że nadal są to bardzo niebezpieczne maszyny i żadne środki bezpieczeństwa zastosowane w aplikacji nie zmniejszą do zera ryzyka urazów dla obsługi.
Autor: Kamil Wójcik, International Machinery Safety Expert, CMSE ® Pilz Polska
Źródło: Pilz Polska
- Roboty mobilne - przegląd rynku 2020
- Praktyczna wiedza od ekspertów Beckhoff
- Robotyzacja zakładów mięsnych: Moda czy innowacja?
- 212 mln zł na automatyzację i robotyzację dla MŚP
- Hybrydowe zgrzewanie punktowe materiałów MPMS/MPC
- P-Weld – Zrobotyzowane Rozwiązania w Spawaniu
- Ulga na robotyzację - do kiedy można skorzystać?
- Zrobotyzowany przegląd targów branżowych 2025
- Webinary Beckhoff – dostępne online
- Estun inwestuje w Polsce
- Raport: Przegląd Rynku Robotów Współpracujących (Cobotów)
- Jak zwiększyć efektywność AGV? Radarowe czujniki w akcji
- Raport: Rynek robotów mobilnych AGV i AMR w 2025
- Nowe funkcje usprawniają pracę inżynierów i programistów
- Monitorowanie i optymalizacja flot robotów
- Konkretnie o Automatyzacji – praktyczne spotkania dla przemysłu
- Moduły liniowe Bosch Rexroth przyspieszają automatyzację
- Jak wybrać system ERP idealny dla firmy produkcyjnej?
- EMO Hannover 2025 – odwiedź centrum innowacji przemysłowych
- Automatyzacja sprzątania z KIRA CV
- Rekordowe targi robotyki i automatyzacji automatica 2025
- Rynek robotów współpracujących — perspektywy na rok 2025
- Dyrektywa maszynowa 2023/1230: Co zmienia się od 2027?
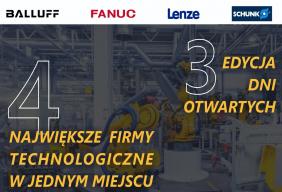
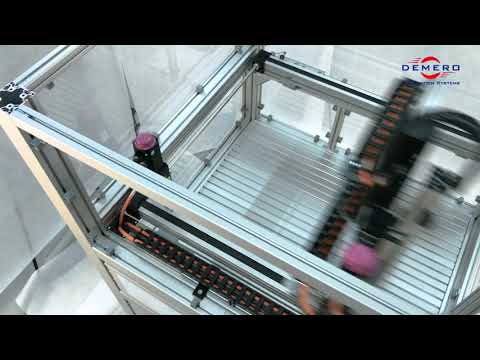
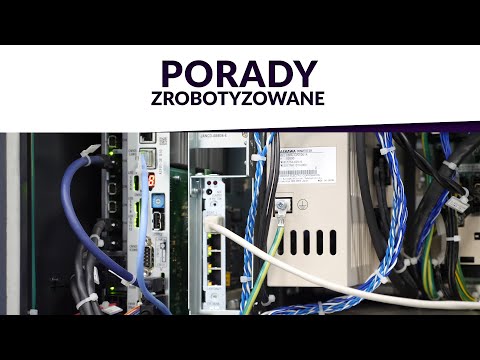

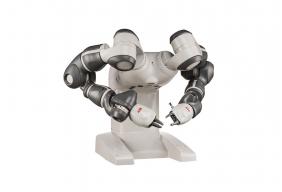
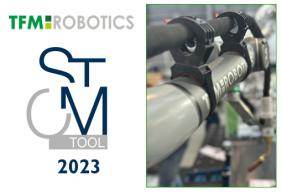