Fabryka Przyszłości to udoskonalanie procesów produkcyjnych
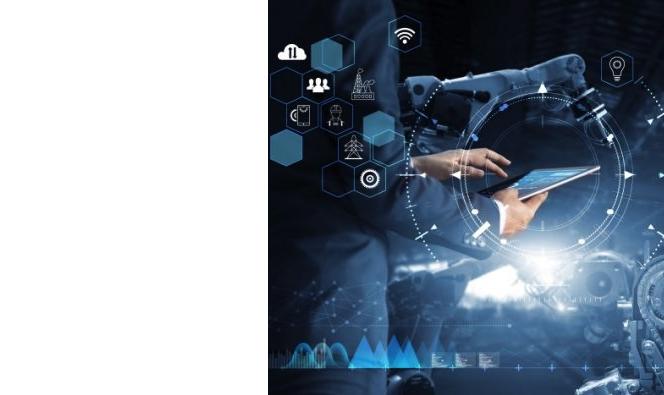
W fabryce wdrażającej standardy Przemysłu 4.0 przepływ danych następuje w dokładnie określony sposób. Pierwszym etapem jest zbieranie danych ze wszystkich możliwych źródeł. Spora część pochodzi ze standardowych urządzeń: pulpitów operatorskich, napędów, sterowników PLC. Niektóre wymagają zainstalowania dodatkowych czujników albo zintegrowania z systemami zarządzającymi budynkiem (automatyka ogrzewania, wentylacji, klimatyzacji).
Zebrane dane są przesyłane do urządzeń brzegowych (Edge Computing), w których mogą być częściowo interpretowane, poddawane analizie statystycznej. Mogą też zasilać aplikacje wykorzystujące sztuczną inteligencję i w ten sposób wspomagać zarządzanie procesami na poziomie hali produkcyjnej.
Kolejnym etapem jest transmisja danych z warstwy Edge do systemu IT firmy. Z reguły trafiają one do baz danych, coraz częściej realizowanych nie przy pomocy tradycyjnych serwerów, a w chmurze udostępnianej przez zewnętrzną firmę.
Dane zebrane w bazach mogą być dowolnie przeglądane, analizowane i interpretowane. Służą do planowania działań w dłuższej perspektywie, wyszukiwania powtarzających się problemów itp. Niezastąpionymi narzędziami analitycznymi są aplikacje dostarczające danych w postaci graficznej. Z reguły są one projektowane jako aplikacje webowe, dzięki czemu procesy mogą być kontrolowane praktycznie z dowolnego miejsca na świecie, na przykład w porozumieniu z producentem maszyn.
Ostatecznym etapem, zamykającym pętlę sprzężenia zwrotnego, jest podejmowanie bezpośrednich działań poprawiających produkcję. Być może w fabrykach przyszłości ten proces będzie się odbywał w większości bez udziału „czynnika ludzkiego”.
![]() |
Filozofia ciągłego udoskonalania procesu pracy – Kaizen
Produkcja jest nierozerwalnie związana z kontrolą jakości. Każde przedsiębiorstwo, o ile chce się utrzymać na rynku, musi weryfikować swoje wyroby, zanim opuszczą one fabrykę. Sprzedaż wadliwych produktów oznacza kłopoty: utratę zaufania, koszty obsługi zwrotów, reklamacji, kary umowne. Kontrolują wszyscy: od rzemieślników po wielkie koncerny, jednak mechanizmy i cel kontroli mogą być bardzo odmienne.
W przypadku prostego produktu, który nie ma wpływu na zdrowie i bezpieczeństwo ludzi albo przebieg procesów biznesowych o wielkiej wartości, można poprzestać na prostym sprawdzeniu zgodności z projektem. Można nawet zrezygnować z kontroli każdego egzemplarza, poprzestając na wyborze losowych sztuk. Takie podejście jest rozsądne przy produkcji gwoździ, patyczków do szaszłyków, wielu produktów spożywczych i dopuszcza pojawienie się na rynku pewnej liczby wadliwych produktów.
Inaczej jest w przypadku przedmiotów skomplikowanych, których wady prawdopodobnie będą miały poważne konsekwencje: stymulatory serca, silniki lotnicze czy implanty są badane i testowane z niezwykłą starannością, bez przyzwolenia na wysłanie klientowi choćby jednego niezgodnego z wymaganiami egzemplarza.
Przyczyna różnicowania kryteriów i sposobów kontroli jakości jest oczywista: jest to czasochłonny, kosztowny proces, a koszty należy trzymać w ryzach. Po dokładniejszej analizie okaże się jednak, że odpowiedź na pytanie: czy warto dokładnie kontrolować jest bardziej skomplikowana i zależy w dużym stopniu od odpowiedzi na pytanie: jak wykorzystamy informacje uzyskane podczas kontroli?
Jeśli sprawdzamy jakość po to, by odrzucić wadliwe egzemplarze i na tym poprzestajemy, wówczas realizujemy podstawowy cel ochrony przed utratą reputacji i kosztami zwrotów, ale nie wykorzystujemy w pełni potencjału informacji, które zdobywamy. Dowiadujemy się, że coś poszło nie tak, jak powinno, ale rezygnujemy z postawienia jednego z najważniejszych pytań w historii ludzkości: dlaczego? Nie wyciągamy wniosków z błędów i zgadzamy się na to, że będą się powtarzały. Za pieniądze wydane na kontrolę jakości dostajemy mniej niż moglibyśmy dostać.
A gdyby postawić sobie za cel maksymalne wykorzystanie informacji o problemach z jakością i postanowić, że żadnej niedoskonałości produktu nie pozostawimy bez poznania jej przyczyn? A kiedy już poznamy te przyczyny, natychmiast zmodyfikujemy proces lub maszyny tak, żeby zapobiec powtarzaniu się problemu? Cóż, wtedy zastosujemy filozofię Kaizen: ciągłego doskonalenia jakości i redukcji strat powodowanych przez błędy.
Konsekwentne wdrażanie tej filozofii teoretycznie powinno doprowadzić do powstania produktu doskonałego: pozbawionego wad, idealnie zgodnego z projektem, wytworzonego najniższym możliwym kosztem. Tak byłoby w świecie idealnym, w którym cały proces produkcji można poddać ciągłej, nieskończenie dokładnej kontroli, a każde zidentyfikowane odstępstwo od normy natychmiast identyfikujemy i usuwamy jego przyczynę.
W rzeczywistym świecie fabryki, z jego wysoką dynamiką, wpływem procesów stochastycznych, zależnością od czynników zewnętrznych (dostawców surowców, podzespołów, energii), nie jest to możliwe, ale warto się starać, tym bardziej że czwarta rewolucja przemysłowa dostarcza narzędzi, które ułatwiają dążenie do ideału.
Klasyczne wdrożenie Kaizen wyglądało mniej więcej tak. Wszyscy pracownicy byli instruowani, że mają zwracać szczególną uwagę na jakość produktów i reagować na wszelkie zauważone odstępstwa od normy. Jeśli na taśmie produkcyjnej pojawi się wadliwy detal, należy zatrzymać taśmę i poinformować przełożonego, który oceni sytuację i rozpocznie poszukiwanie przyczyny. Nawet jeśli nie zidentyfikuje jej natychmiast, zgromadzi informacje umożliwiające usunięcie problemu w najbliższej przyszłości.
W praktyce bywa różnie. Pracownicy nie wszystko zauważają, a nawet jeśli zauważają, czasami mają opory przed zgłaszaniem problemów. Zatrzymanie linii wiąże się z kosztami, spada wydajność, wskaźniki lecą w dół.
Przemysł 4.0 podsuwa rozwiązanie: automatyczna, obiektywna kontrola na każdym etapie wytwarzania likwiduje problem obawy przed podjęciem decyzji o zgłoszeniu incydentu. Analiza strumienia danych przesyłanego przez maszyny w czasie rzeczywistym umożliwia skojarzenie wybrakowanego detalu z warunkami pracy maszyn i wpływem środowiska.
Jeśli dodamy do tego przemyślany, funkcjonalny interfejs, prezentujący graficznie stan faktyczny w zestawieniu z pożądanymi wartościami parametrów, to otrzymamy narzędzie umożliwiające znaczne przyspieszenie cyklu Kaizen: od wykrycia problemu do implementacji rozwiązania. To rozwiązanie będzie działało nawet w przypadku bliskim modelowi tradycyjnemu, kiedy linia jest nadzorowana przez operatora – człowieka. Jego decyzje będą miały solidne podstawy w postaci zarejestrowanych danych, maleje więc stres związany z podejmowaniem odważnych decyzji o zatrzymywaniu produkcji.
Podstawowym warunkiem automatyzacji kontroli jakości i diagnostyki linii jest transmisja danych z maszyny do systemu IT za pośrednictwem jednego z rozwiązań klasy Edge. Mitsubishi Electric oferuje rozwiązania sprzętowe (modemy dostępowe np. eWon, MES Interface, MES IT, komputery przemysłowe MELIPC) i programowe (MAPS Agent Server, DeviceWise Enterprise Gateway). To ostatnie oprogramowanie wraz z komputerem MELIPC tworzy gotowe wszechstronne rozwiązane o nazwie MESUS.
Kluczem do sukcesu są: nieprzerwane zbieranie danych, ciągła analiza i konsekwentne likwidowanie przyczyn. W praktyce trzeba szukać kompromisów, ale jest to typowe dla większości zadań inżynierskich: najważniejsza jest optymalizacja. Usunięcie wszystkich potencjalnych przyczyn błędów jest niemożliwe, trzeba się skoncentrować na najważniejszych. W tym miejscu z pomocą przychodzi zasada PARETO. Można założyć, że 20% przyczyn odpowiada za 80% kosztów związanych z wadami. 20% brzmi zupełnie nieźle, ponieważ można oczekiwać, że zlikwidowanie choćby 10% przyczyn przyniesie wymierny efekt finansowy i wizerunkowy.
Dobrym przykładem skutecznego usuwania problemów, których identyfikacja jest niemożliwa, a w każdym razie bardzo trudna przy pomocy konwencjonalnych metod, są mikroprzestoje. Teoretycznie każdy cykl pracy maszyny powinien wyglądać identycznie: każdy ruch powinien trwać tyle samo, odbywać się z identyczną prędkością, przyspieszeniem. W rzeczywistości elementy wykonawcze: napędy, silniki, serwomechanizmy pracują „nierówno”. Zdarza się, że jeden na kilka lub kilkanaście cykli jest nieco dłuższy. Mówimy o różnicach rzędu części sekundy, ale biorąc pod uwagę fakt, że maszyna może wykonywać wiele tysięcy cykli w jednostce czasu, opóźnienia kumulują się i mogą sięgać wielu minut.
Mikroprzestoje są trudne do zauważenia, sprawę komplikuje dodatkowo fakt, że występują losowo. Ratuje nas statystyka: obserwacja zachowania maszyny w dłuższym czasie i pomiar każdego pojedynczego cyklu umożliwia wykrycie problemu i przyczyny: zużycia powierzchni ślizgowych, wahań ciśnienia powietrza, zabrudzenia elementów ruchomych.
e-Factory Information Center
Mitsubishi Electric rozwija wiele narzędzi ułatwiających implementowanie zasad Przemysłu 4.0 w fabrykach różnej wielkości, o praktycznie dowolnym profilu produkcji. Do grupy najważniejszych i najbardziej wszechstronnych należy e-Factory Information Center. Jest to system klasy MES (Manufacturing Execution System), zaprojektowany jako modułowe, łatwo skalowalne narzędzie typu „All in One”.
Dzięki takiemu podejściu można zacząć czerpać korzyści ze stosowania e-Factory na dowolnym etapie rozwoju biznesu i dostosowywać system do zmieniających się potrzeb wynikających z charakteru i skali prowadzonej działalności. Podstawowym zadaniem e-Factory jest redukcja strat.
![]() |
Ogólnie rzecz ujmując, systemy MES są budowane po to, żeby monitorować produkcję w czasie rzeczywistym, dostarczać informacje o stanie maszyn i całego zakładu produkcyjnego, obliczać faktyczny całkowity czas pracy urządzeń i wskaźnik OEE. Zdecydowanie ułatwiają planowanie produkcji (w tym kolejność wykonywanych zadań), kontrolę jakości, nadzór nad dokumentacją.
MES są niezbędnym elementem fabryki przyszłości, dlatego Mitsubishi Electric przykłada szczególną wagę do ich optymalizacji i aktualizacji. Bieżące wersje systemu są w pełni kompatybilne z urządzeniami dostarczanymi przez Mitsubishi Electric i wielu innych producentów sprzętu dla automatyki przemysłowej.
e-Factory Information Center może mierzyć ponad 20 KPIs (Key Performance Indicators), między innymi: czas przestojów, wolumen produkcji, czas produkcji, jednostkowy koszt wytworzenia, zużycie energii, realizację wyznaczonych celów, współczynnik OEE i wiele innych. System ma otwartą architekturę, dzięki czemu Mitsubishi Electric może korzystać z doświadczenia współpracujących firm, specjalizujących się np. w rozwijaniu narzędzi wykorzystujących sztuczną inteligencję.
Dane zbierane z urządzeń na linii produkcyjnej są przesyłane do modułów, które je przetwarzają i udostępniają w postaci maksymalnie ułatwiającej interpretację. Przekłada się to na szybkość podejmowania decyzji i ich skuteczność.
OEE – wskaźnik wydajności dla procesów produkcyjnych
Jednym z najważniejszych wskaźników obliczanych przez e-Factory Information Center jest OEE (Overall Equipment Effectiveness – całkowita efektywność wyposażenia). Przy okazji wyznaczane są inne wskaźniki, np. straty czasu spowodowane przestojami i mikroprzestojami.
Nadrzędnym celem monitorowania OEE jest wyeliminowanie sześciu wielkich strat:
- straty dostępności spowodowanej nieplanowanymi i planowanymi zatrzymaniami,
- straty wydajności, za którą odpowiadają między innymi mikroprzestoje oraz zwolnione cykle,
- straty jakości pojawiające się w wyniku powstawania odrzutów po produkcji, strat na materiale w czasie uruchamiania.
![]() |
Eco-monitoring
Nadzorowanie procesów produkcji przynosi wiele korzyści. Jednym z możliwych zastosowań danych pochodzących z maszyn i infrastruktury zainstalowanej w hali produkcyjnej jest pomiar efektywności energetycznej. Dzięki precyzyjnym pomiarom wiadomo, w jaki sposób dystrybuowana jest energia, gdzie pojawiają się straty, kiedy występują maksymalne i minimalne zużycia energii.
Te informacje są niezwykle ważne dla energetyków i technologów, którzy mogą je wykorzystać do planowania produkcji w taki sposób, żeby maksymalnie wykorzystywała warunki umowy z dostawcą energii elektrycznej (zniżki za korzystanie z energii poza godzinami największego obciążenia sieci energetycznej itp.).
Identyfikacja urządzeń i procesów, które są zbyt energochłonne, przynosi nie tylko korzyści finansowe. Pozwala zmniejszyć zużycie energii, a więc pośrednio także obciążenie środowiska naturalnego kosztami jej wytworzenia (przede wszystkim emisją dwutlenku węgla).
Kaizen w Fabryce Przyszłości
Można sobie wyobrazić, że fabryki przyszłości będą implementowały rozwiązania o znacznie większym stopniu samodzielności. Gdyby maszyna, która stwarza problemy, „potrafiła” się sama naprawić, a w każdym razie skalibrować czy „dostroić”, zrobilibyśmy kolejny wielki krok na drodze ku fabrykom autonomicznym: przyjmującym zlecenie i realizującym je bez udziału człowieka. W tej chwili to utopia, ale, trzeba przyznać, dość kusząca.
Źródło: Mitsubishi Electric Europe
Redaktor: MRR
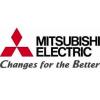
32-083 Balice
+48 12 630 47 41
- Roboty mobilne - przegląd rynku 2020
- Praktyczna wiedza od ekspertów Beckhoff
- Robotyzacja zakładów mięsnych: Moda czy innowacja?
- 212 mln zł na automatyzację i robotyzację dla MŚP
- Hybrydowe zgrzewanie punktowe materiałów MPMS/MPC
- P-Weld – Zrobotyzowane Rozwiązania w Spawaniu
- Ulga na robotyzację - do kiedy można skorzystać?
- Zrobotyzowany przegląd targów branżowych 2025
- Raport: Przegląd Rynku Robotów Współpracujących (Cobotów)
- Raport: Rynek robotów mobilnych AGV i AMR w 2025
- Jak wybrać system ERP idealny dla firmy produkcyjnej?
- EMO Hannover 2025 – odwiedź centrum innowacji przemysłowych
- Rynek robotów współpracujących — perspektywy na rok 2025
- Dyrektywa maszynowa: Co zmienia się od 2027 w robotyzacji?
- Rynek robotów przemysłowych: silne odbicie w 2025?
- Wsparcie procesu robotyzacji w Polsce. Rekomendacje PIE
- OEE i śledzenie przestojów
- TOOLEX i ExpoWELDING 2025. Katowice znów stolicą przemysłu
- Współpraca BMW i SEW-EURODRIVE
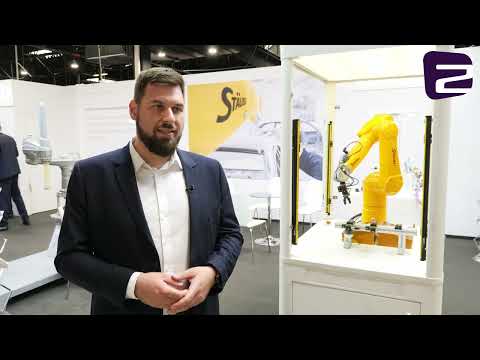
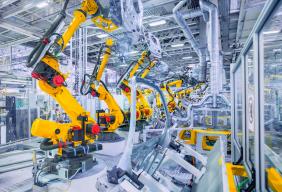

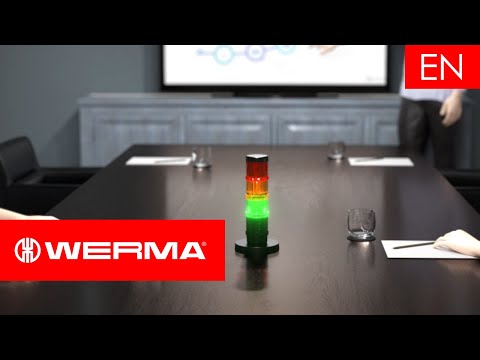
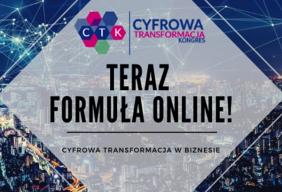
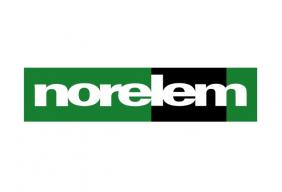