Pięć przeszkód na drodze do IIoT
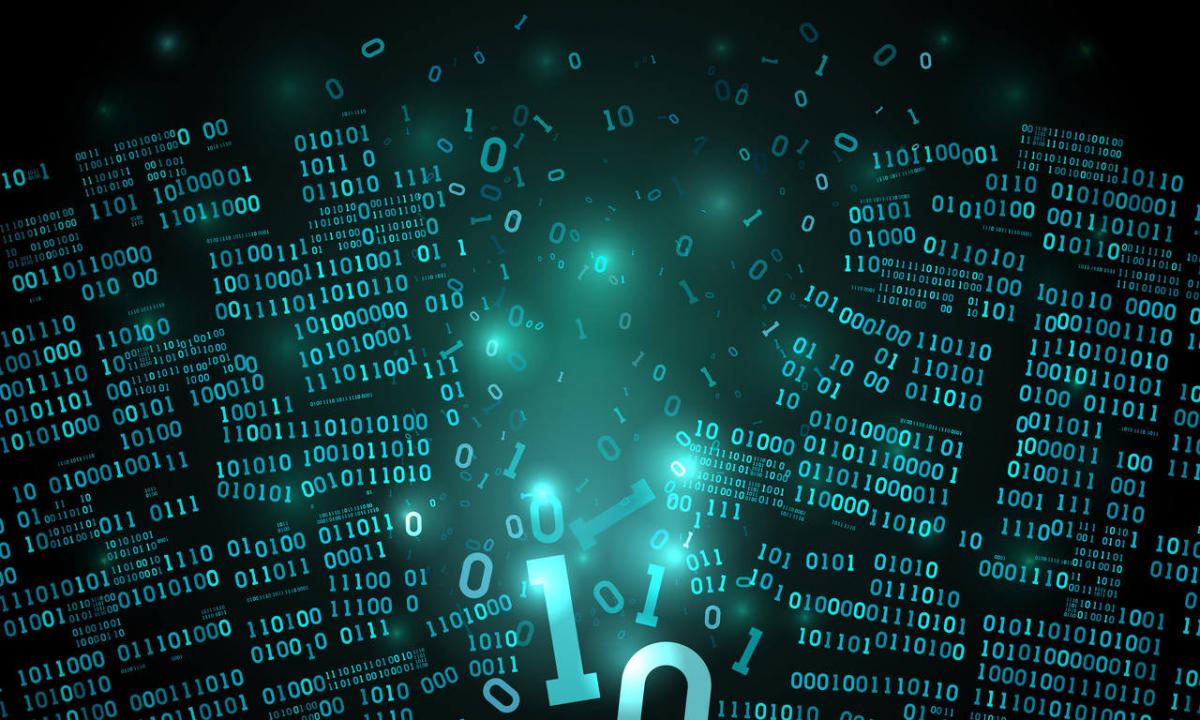
Przemysł 4.0 (Industry 4.0) , przemysłowy internet rzeczy (IIOT) lub fabryka przyszłości: Coraz więcej użytkowników przemysłowych myśli o cyfryzacji procesów produkcyjnych.
Nie ma magicznej formuły dla tej transformacji. Ale lepiej nie popełniać różnego rodzaju błędów po drodze. Bosch Rexroth ma już ponad pięć lat doświadczenia we wdrażaniu koncepcji Industry 4.0, która została nabyta w wyniku działań własnych i zewnętrznych. W ramach tego procesu specjaliści od automatyzacji firmy zidentyfikowali pięć największych przeszkód, które utrudniają wprowadzenie Internetu Rzeczy (IOT) i podnoszą koszty.
1. Brak planowania: gromadzenie danych bez żadnych skutków
Dane są punktem wyjścia do usieciowanej produkcji i ciągłego doskonalenia. Brzmi nieźle. Jednak użytkownicy nadal chętnie korzystają z dużej liczby czujników i zbierają miliardy bitów danych, które są następnie analizowane przy użyciu standardowego oprogramowania IT.
Problem: Standardowe oprogramowanie nie rozpoznaje określonych maszyn i procesów i daje jedynie pozornie znaczące wyniki. Aby naprawdę wiedzieć, które informacje są ważne, pracownicy muszą być zaangażowani w proces i mieć możliwość dzielenia się swoją wiedzą i doświadczeniem. Główny sposób poprawa przejrzystości wszystkich procesów to wizualizacja informacji. Pracując w systemie zamkniętym, pracownicy mogą naprawdę zidentyfikować ważne wyniki i optymalizacja procesu pomiarowego. Doświadczenie jednak pokazuje: Nie wystarczy skupić się na produkcji. To raczej holistyczne podejście zapewnia dodatkowe informacje dotyczące logistyki, zakupów, rozwoju oraz wszelkich innych funkcji firmy.
2. Przecenianie możliwości: mieć wszystko od razu
Niektórzy użytkownicy chcą zrobić wszystko za jednym razem, wprowadzenie koncepcji Przemysłu 4.0 w jednym głównym projekcie i jednocześnie korygując wszelkie niedociągnięcia. To dość ryzykownee podejście, które znacznie komplikuje proces. W rezultacie bezpośrednie ustalenie przyczyn i skutków staje się trudne. Ponadto takie podejście często prowadzi do przeinwestowania, co szybko sprawia wrażenie że cyfrową transformację można osiągnąć jedynie poprzez wprowadzenie nowych systemów i maszyn. Sposób małych kroków jest najbardziej skuteczny. Wyniki można uzyskać w projektach pilotażowych bądź konkretny i optymalizuj krótkie działania Zamknięte. Jednocześnie proces ten stopniowo wprowadza pracowników w temacie i zwiększa ich zaangażowanie. Takie projekty pilotażowe często pokazują, że można łatwo połączyć dostępne maszyny i systemy.
3. Niewłaściwe podstawy: używanie niewłaściwego standardu
Niektórzy producenci maszyn i użytkownicy końcowi zbyt wcześnie wybierają standard na przyszłość. Jest to nieprzemyślany ruch, ponieważ normy w Industry4.0 ciągle się zmieniają. Jedyną pewną rzeczą jest sama zmiana. Maszyna przygotowana na przyszłość musi być połączona i nie może spełniać tylko obecnych standardów, ale musiumożliwiaćłatwą modyfikację w odpowiedzi na przyszłe zmiany. Użytkownicy mogą zabezpieczyć swoje wcześniejsze inwestycje tylko poprzez otwartość i elastyczność.
4. Wynaleźć koło od nowa: programowanie wszystkiego samodzielnie
Można je znaleźć w wielu firmach: majsterkowicze, którzy doskonale wymyślają dopasowane rozwiązania do potrzeb wewnętrznych. To ryzykowne oferta. Takie podejście pochłania ogromną ilość czasu i pieniędzy. Dokumentacja własnego rozwiązania toczy się w nieskończoność, nie wspominając o standardzie rozwiązania, który jest znacznie bardziej przyjazny dla użytkownika.Dzięki standardowym rozwiązaniom użytkownicymogą podłączyć maszyny w ciągu kilku godzin i centralnie zarządzać wszystkimi urządzeniami IoT w sieci. Jeszcze jeden ważny wniosek: mieszanie funkcji maszyny IoT w systemie sterowania maszyny powodują niepotrzebne komplikacje. Dostępne są opcje aktualizacji ograniczone ze względu na potrzebę zapewnienia bezpieczeństwa i orzecznictwo. Z tego powodu sensowniej jest obsługiwać funkcje Internetu Rzeczy za z wykorzystaniem dedykowanych systemów i skupienie się na komunikacji w czasie rzeczywistym między systemami.
5. Nic się nie stanie: lekceważenie względów bezpieczeństwa
Liczby te dają nam do myślenia: ponad 50% firm biorących udział w ankiecie przyznaje, że nie czują się przygotowane do obrony przed atakami wymierzonymi w ich systemy IoT. 94% z nich przewiduje, że ich podatność na zagrożenia będzie się jeszcze zwiększać. Mają rację, jednak istnieją sprawdzone procesy w zakresie bezpieczeństwa IT, które można szybko i łatwo rozszerzyć na produkcję, jak np. segmentacja sieci oraz zapory firewall. Instrumenty, które mogą być szczególnie przydatne totakie, którymiużytkownicymogącentralnie zarządzać wszystkimi systemami IoT i jednocześnie aktualizować zabezpieczenia we wszystkich lokalizacjach na całym świecie. To działanie zabezpiecza operacje realizowane w ramachprodukcjisieciowej.
Źródło: Bosch Rexroth
- Roboty mobilne - przegląd rynku 2020
- Praktyczna wiedza od ekspertów Beckhoff
- Robotyzacja zakładów mięsnych: Moda czy innowacja?
- 212 mln zł na automatyzację i robotyzację dla MŚP
- Hybrydowe zgrzewanie punktowe materiałów MPMS/MPC
- P-Weld – Zrobotyzowane Rozwiązania w Spawaniu
- Ulga na robotyzację - do kiedy można skorzystać?
- Zrobotyzowany przegląd targów branżowych 2025
- Webinary Beckhoff – dostępne online
- Estun inwestuje w Polsce
- Raport: Przegląd Rynku Robotów Współpracujących (Cobotów)
- Jak zwiększyć efektywność AGV? Radarowe czujniki w akcji
- Raport: Rynek robotów mobilnych AGV i AMR w 2025
- Nowe funkcje usprawniają pracę inżynierów i programistów
- Monitorowanie i optymalizacja flot robotów
- Konkretnie o Automatyzacji – praktyczne spotkania dla przemysłu
- Moduły liniowe Bosch Rexroth przyspieszają automatyzację
- Jak wybrać system ERP idealny dla firmy produkcyjnej?
- EMO Hannover 2025 – centrum innowacji przemysłowych
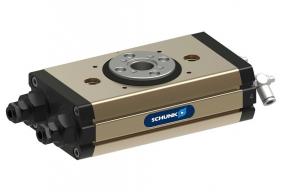
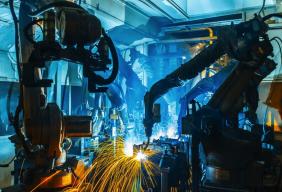

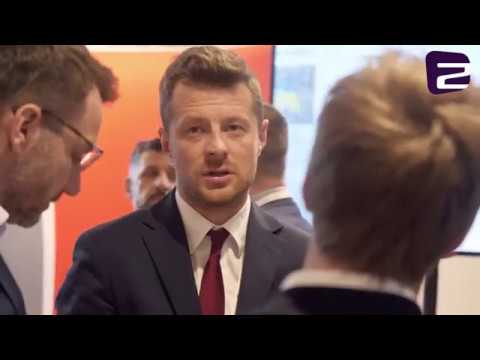
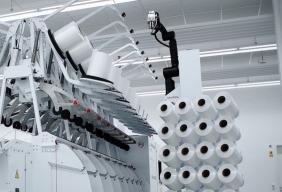
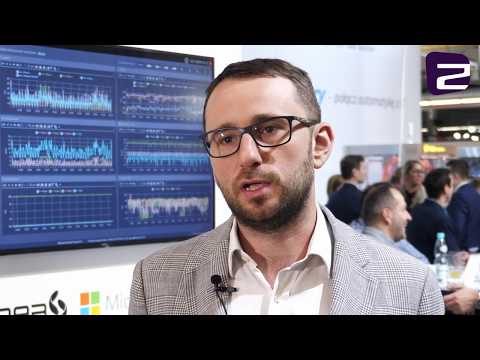