Diagnostyka drganiowa obrabiarek i procesów
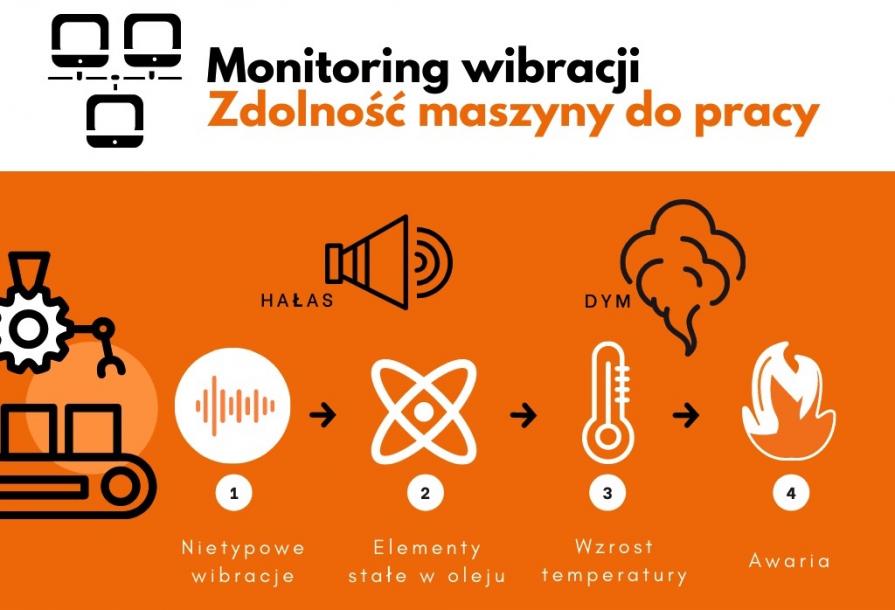
![]() |
Zużycie maszyn jest wynikiem aż 85 % ich postojów. Ponieważ trudno wyobrazić sobie bez nich nowoczesne metody produkcji, konieczna jest skuteczna diagnostyka, aby utrzymać ich efektywność na jak najwyższym poziomie. Mogą to zapewnić czujniki wibracji, które zapewniają precyzyjną pracę obrabiarki.
Obecny sposób zarządzania parkami maszynowymi wymaga nowych standardów. Zdaniem ekspertów nie da się poprawić wydajności, niezawodności i jakości produkowanych elementów bez głębszej wiedzy na temat poszczególnych części maszyny. Zależy nam na tym, aby maszyna sama się zdiagnozowała. Ponadto, chcemy mieć te informacje w czasie rzeczywistym i z wyprzedzeniem reagować na potencjalnie zbliżające się zagrożenia.
W dobie wszechobecności Internetu wydaje się, że nie ma problemu z pobieraniem danych z maszyn. Okazuje się, że nie jest to takie łatwe.
- W tym obszarze firmy mierzą się z dwoma podstawowymi problemami - twierdzi Marek Maciejewski z ifm electronic. - Pierwszy z nich dotyczy tego, w jaki sposób możemy dane pozyskać z maszyny i które z nich są naprawdę istotne. Natomiast druga wątpliwość dotyczy tego, jak te dane należy interpretować. |
Informacja właśnie wtedy, kiedy jest potrzebna
Ważne jest, aby pamiętać, że dla predykcyjnego utrzymania ruchu należy stworzyć odpowiednią strategię, którą buduje się przez lata. Jest to proces, którego celem jest uzyskanie informacji o stanie maszyny, dokładnie wtedy, gdy jest to potrzebne. Kluczem jest odpowiednia reakcja, czyli podjęcie działań zapobiegających nieplanowanym przestojom.
Monitorowanie wibracji jest dobrym wskaźnikiem formy maszyny. Nieprawidłowe wibracje mogą wskazywać na uszkodzenie, poluzowanie lub tarcie poszczególnych części urządzenia, niewłaściwe ustawienie, niewspółosiowość, degradację łożysk, kawitację oraz uszkodzenie taśmy lub elektrycznych części silnika.
Dowiedz się, co naprawić, zanim się zepsuje
Dzięki analizie drgań można przewidzieć uszkodzenie maszyn. Zostanie to pokazane na przykładzie obrabiarki. Wszystkie jej części m.in. wrzeciono, głowica, narzędzie do obróbki, podajnik czy przenośnik łańcuchowy na odpady metalowe, mają mniejszy lub większy wpływ na działanie maszyny. Jakość jej pracy, niezawodność i wydajność zależy właśnie od nich. Aby dowiedzieć się, co należy naprawić, zanim urządzenie ulegnie awarii, niezbędne są informacje o stanie wszystkich jego elementów składowych. Pomocna może być również historia zdarzeń każdej części danej maszyny.
- Dzięki diagnostyce drganiowej można monitorować np. wrzeciono obrabiarki, które jest najbardziej newralgicznym urządzeniem w maszynie - mówi Marek Maciejewski. - Jego nieprawidłowa praca prowadzi do produkowania odpadów, a uszkodzenie łożysk może zatrzymać maszynę na wiele godzin. Niewykryte w porę kolizje mogą doprowadzić do kosztownych uszkodzeń narzędzi i produkowanych detali. |
Przy monitoringu stanu wrzecion sprawdza się diagnostyka drganiowa ifm Octavis. Może dostarczyć informacji na temat kondycji łożysk, niewyważeniu, wykrywaniu kolizji, a następnie analizę narzędzia. Kolizja może zostać wykryta błyskawicznie, w czasie 1-2 ms. Jednak to rozwiązanie powinno być dostosowane do maszyny i jej otoczenia, aby zminimalizować ryzyko fałszywych alarmów.
ifm electronic stworzyło specjalne czujniki, które można łatwo zamontować na wrzecienniku. Lokalizacja instalacji umożliwia precyzyjne wykrywanie drgań i ich zmiany oraz przekazywanie ich do jednostki przetwarzającej. Tam przeprowadzane są wszystkie niezbędne obliczenia, które następnie przetwarzane są w odpowiednie wartości, np. prędkość skuteczną drgań lub wartość szczytową przyspieszeń.
Smartobserver to narzędzie, które dostarcza informacji o aktualnym stanie maszyn. Umożliwia zbieranie i podgląd danych w dowolnym miejscu, a także analizuje pozyskane informacje. Dzięki niemu możliwe jest również sterowanie powiadomieniami np. przez SMS lub email, a także zarządzanie pracami serwisowymi i raportowanie.
Znaczna redukcja kosztów
Podstawowym celem monitorowania maszyn jest ograniczenie niepotrzebnych kosztów związanych z przestojami, konserwacją, a nawet wymianą sprzętu. Jednocześnie istnieją trzy możliwości obniżenia tych wydatków. Pierwsza to konserwacja predykcyjna, czyli poznanie aktualnego stanu urządzenia. Kolejny to jakość procesu np. jeżeli parametry cięcia zmieniają się w wyniku zużycia narzędzia, będzie to sygnalizowane. Trzeci element to zabezpieczenie maszyny. W razie potrzeby może ona zostać zatrzymana awaryjnie, unikając w ten sposób uszkodzenia.
- Wielu dużych użytkowników, zwłaszcza z branży motoryzacyjnej stosuje te rozwiązania od dawna, ponieważ zauważyli tu wielki potencjał oszczędnościowy - mówi Marek Maciejewski. - Jeden z naszych klientów, właśnie z tego sektora, poprzez zainstalowanie systemu monitoringu wrzecion na obrabiarkach ma obecnie pod kontrolą stan swoich maszyn. Wcześniej wymiana narządzi była konieczna co roku, a dzięki zainstalowaniu monitoringu drgań, po trzech latach użytkowania, system pokazuje, że urządzenia są nadal sprawne. Biorąc pod uwagę, że koszt wymiany narzędzi na jednej maszynie to około 20 tys. euro, uzyskane oszczędności są naprawdę spore. |
Potrzebna odpowiedź
Dzięki licznym czujnikom mierzącym czynniki wpływające na pracę maszyny, można uzyskać kilkadziesiąt różnych parametrów.
- Jednak często nikt szczególnie nie kwapi się, aby codziennie analizować przebiegi - mówi Marek Maciejewski. - Często słyszę od firm, że choć zbierają dane z systemów, to korzystają z danych dopiero po zaistnieniu awarii, a to duży błąd. Nawet wczesne informowanie o zbliżającej się katastrofie nic nie da, jeśli nie będzie odpowiedniej reakcji. Tymczasem monitorowanie maszyn może pomóc zapobiec wielu awariom i ograniczyć kosztowne naprawy i przestoje. |
Nowoczesne przedsiębiorstwa produkcyjne mierzą efektywność użytkowania maszyn i urządzeń przy pomocy wskaźnika OEE - Overal Equipment Effectiveness. Zależy on od czasu pracy maszyny, jakości produktu oraz produktywności. ifm electronic dostarcza istotne dane w czasie rzeczywistym dla tych wszystkich obszarów.
Źródło: ifm electronic
Redaktor: MRR
- Roboty mobilne - przegląd rynku 2020
- Praktyczna wiedza od ekspertów Beckhoff
- Robotyzacja zakładów mięsnych: Moda czy innowacja?
- 212 mln zł na automatyzację i robotyzację dla MŚP
- Hybrydowe zgrzewanie punktowe materiałów MPMS/MPC
- P-Weld – Zrobotyzowane Rozwiązania w Spawaniu
- Ulga na robotyzację - do kiedy można skorzystać?
- Zrobotyzowany przegląd targów branżowych 2025
- Webinary Beckhoff – dostępne online
- Estun inwestuje w Polsce
- Raport: Przegląd Rynku Robotów Współpracujących (Cobotów)
- Jak zwiększyć efektywność AGV? Radarowe czujniki w akcji
- Raport: Rynek robotów mobilnych AGV i AMR w 2025
- Nowe funkcje usprawniają pracę inżynierów i programistów
- Monitorowanie i optymalizacja flot robotów
- Konkretnie o Automatyzacji – praktyczne spotkania dla przemysłu
- Moduły liniowe Bosch Rexroth przyspieszają automatyzację
- Jak wybrać system ERP idealny dla firmy produkcyjnej?
- EMO Hannover 2025 – odwiedź centrum innowacji przemysłowych
- Automatyzacja sprzątania z KIRA CV
- Rekordowe targi robotyki i automatyzacji automatica 2025
- Rynek robotów współpracujących — perspektywy na rok 2025
- Dyrektywa maszynowa 2023/1230: Co zmienia się od 2027?
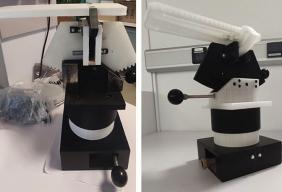

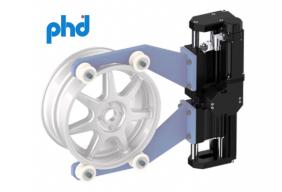
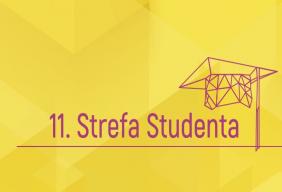

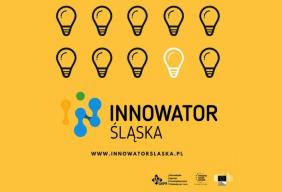