OMRON poprawia wydajność linii produkcyjnej w branży spożywczej

Cleca, znana z produkcji dań słodkich i słonych, wybrała OMRON i jego nową usługę analizy danych IoT, aby zoptymalizować wydajność linii produkcyjnej bulionu. Modernizacja przeprowadzona bez instalowania nowych urządzeń umożliwiła włoskiej firmie produkcję ponad 800 000 kartonów miesięcznie i zwiększenie wydajności o 8%.
Cleca to włoska firma znana w branży handlu detalicznego na dużą skalę, zarówno we Włoszech, jak i za granicą. Specjalizuje się w szerokim asortymencie produktów spożywczych - w tym produktów słodkich, dań słonych, przypraw i kostek rosołowych - rozprowadzanych pod różnymi markami i spełniających wysokie standardy jakościowe.
W ostatnich latach przedsiębiorstwo dostosowało się do nowych trendów rynkowych, a w szczególności do wysokiego popytu na produkty gotowe do spożycia. Firma koncertuje się głównie na gotowym bulionie - produkcie o dwucyfrowym współczynniku wzrostu sprzedaży, który skłonił włoską firmę do dokonania przeglądu jej infrastruktury technologicznej.
Pomocnikiem firmy Cleca na jej drodze do modernizacji technologicznej był zespół OMRON-u, a w szczególności specjalistyczny zespół, który od lat nadzoruje i-BELT- usługę wykorzystującą reguły Internetu Rzeczy (IoT) i analizę danych w celu poprawy wydajności zautomatyzowanych systemów.
Zamiana inwestycji w maszyny na inwestycję w analizę danych
Celem firmy Cleca w zakresie modernizacji linii produkcyjnej gotowego do spożycia bulionu było osiągnięcie wzrostu o co najmniej 3-4 punkty procentowe w porównaniu z pierwszą linią uruchomioną w 2018 roku. Została ona uznana za niewystarczającą do zaspokojenia rosnącego popytu rynkowego. W początkowej fazie rozważano dwie opcje: remont całej linii poprzez inwestycje w nowe maszyny lub optymalizacja wydajności istniejącego systemu.
„Dzięki zapewnieniom firmy OMRON od razu wybraliśmy drugą opcję – nie tylko ze względu na koszty” - wyjaśnia Michele Franceschini, CIO i dyrektor generalny ds. piekarnictwa w firmie Cleca. „Już na samym początku zdaliśmy sobie sprawę, że tracimy wydajność ze względu na złożoność linii, która zawiera sześć podstacji i całą masę podzespołów różnych marek, a wszystkie te podzespoły muszą się ze sobą komunikować. W związku z tym poprosiliśmy firmę OMRON, aby pomogła nam określić, które części linii były niewystarczająco lub niewłaściwie wykorzystywane”. |
„Oceniliśmy każdy aspekt linii, tak jakby to był łańcuch złożony z kilku ogniw” - wyjaśnia Paolo Cavallanti, kierownik projektu i-BELT w firmie OMRON. „Mamy duże doświadczenie w zakresie procesów odbywających się w różnych maszynach i podstacjach, ale jedynym sposobem na dokładne określenie słabych ogniw łańcucha jest analiza jego wytrzymałości i wydajności. Mimo że ten krok jest kluczowy, to nie wystarczy, aby przejść do kolejnego etapu i dokonać regulacji działania linii. Innym czynnikiem, który należy wziąć pod uwagę, jest sposób, w jaki poszczególne elementy są ze sobą połączone. Wszelkie działania naprawcze mogą w rzeczywistości negatywnie wpłynąć na końcowy rezultat, a nawet na działanie samej linii. Dzięki temu postrzegamy proces nie jako ścieżkę liniową od punktu A do punktu B, ale jako rezultat wynikający ze złożonej sieci obejmującej kilka wejść i wyjść, które określają odporność linii”. |
![]() |
Od danych do produkcji: jak usługa i-BELT zwiększyła wydajność
Linia firmy Cleca jest pierwszą tego typu w Europie linią, która wykorzystuje i-BELT, usługę firmy OMRON obejmującą rozwiązania IoT do gromadzenia, przeglądania i analizowania danych na brzegu sieci w celu optymalizacji procesu produkcyjnego. Inżynierowie skupili się na różnych odcinkach złożonej linii, która obejmuje sześć podstacji – pasteryzacji, napełniania, kapslowania, kontroli RTG, pakowania i paletyzacji. Linia jest dodatkowo wyposażona w wiele podzespołów automatyki na platformie Sysmac, z uwzględnieniem maszyn ze sterownikiem NX1 i serwomotorów serii 1S firmy OMRON.
Plan prac zapewnił możliwość analizy poszczególnych stacji w celu ustalenia, która z nich miała negatywny wpływ na ogólną wydajność produkcji. Podjęto decyzję o zainstalowaniu narzędzi do ciągłego monitorowania, aby analizować system produkcji przez 24 godziny na dobę, zgromadzić dane z każdej stacji i zbadać je w czasie rzeczywistym za pomocą protokołu MQTT.
Analiza danych ujawniła jeden kluczowy problem: istotne wąskie gardło na drugiej stacji, na której znajduje się maszyna do napełniania. W związku z tym dokonano ulepszeń na poziomie zadań, które nie wywierają wpływu na kolejne stacje.
„Wyzwaniem związanym z wdrożeniem tego typu środków jest uniknięcie powstawania blokad lub zatorów na stacjach znajdujących się w dalszej części” - wyjaśnia Andrea Stefani, inżynier produktu w firmie OMRON Automation. „Gdy mamy do czynienia z tak wieloma etapami przetwarzania i maszynami od różnych dostawców, jak w przypadku linii bulionu, istnieje tendencja do pomijania szerszej perspektywy i analizowania poszczególnych procesów, a nie całej linii. Koncepcja i-BELT polega na tym, aby mieć kompleksowy przegląd i kierować się całościowym podejściem do zarządzania linią w sposób, w jaki dyrygent prowadzi orkiestrę”. |
![]() |
Wyniki wykraczające poza oczekiwania
Analiza przeprowadzona zgodnie z modelem i-BELT umożliwiła pracownikom firmy Cleca stopniowe zwiększanie wydajności maszyny do napełniania, co ostatecznie zapewniło wzrost wydajności o 8%. W rezultacie włoska firma może teraz przyjmować około 2 kartony bulionu co sekundę, co daje łącznie ponad 800 000 kartonów miesięcznie.
„Zaangażowanie firmy OMRON i zespołu pracującego nad usługą i-BELT miało kluczowe znaczenie dla nawiązania komunikacji między istniejącymi podzespołami systemu a wszystkimi urządzeniami wykorzystywanymi do gromadzenia danych” - mówi Michele Franceschini. „Stosując to podejście, udało nam się stworzyć linię o bardzo wysokim stopniu szczegółowości i podzielić ją na oddzielne bloki w celu ich indywidualnej analizy i skorelowania z kolejnymi blokami. Można powiedzieć, że dynamika takiej linii jak nasza jest podobna do zarządzania ruchem w korku: kiedy ruch się zatrzymuje i nieoczekiwanie wznawia, a nie odbywa się w sposób płynny, dochodzi do zatorów, które przechodzą na kolejne etapy i spowalniają dalszy proces. Firma OMRON była szczególnie zmotywowana perspektywą zupełnie nowego wyzwania, przynajmniej dla rynku europejskiego” - podsumowuje Paolo Cavallanti. |
Źródło: OMRON
- Roboty mobilne - przegląd rynku 2020
- Przegląd targów branżowych 2024
- Czy powinienem inwestować w robotyzację?
- Przemysłowa Wiosna STOM 2024 zapowiada się wyjątkowo
- Praktyczna wiedza od ekspertów Beckhoff
- Raport PARP: Perspektywa do 2028 roku
- Przemienniki Lenze dla branży klimatyzacyjnej
- O narzędziach i recyklingu na Targach INNOFORM®
- Przemysł i logistyka 4.0 na ITM Industry Europe 2024
- Robotyzacja zakładów mięsnych: Moda czy innowacja?
- 212 mln zł na automatyzację i robotyzację dla MŚP
- Hybrydowe zgrzewanie punktowe materiałów MPMS/MPC
- Dynamiczny rozwój sektora robotyki przemysłowej
- Weź udział w Material Forum 2024
- Wyzwania i Przemiany w Branży Motoryzacyjnej: Raport ABB
- Tajwan dla inteligentnej produkcji na ITM Industry Europe



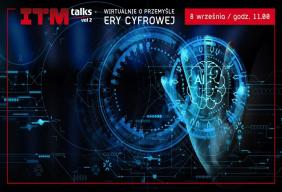
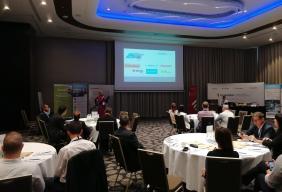
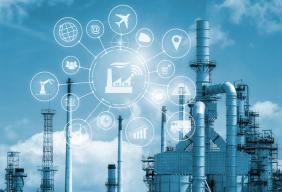